بازرسی سازه های فولادی (مقررات ملی ساختمان و AWS D1.1)
ثبت نام دوره
نوع دوره | تاریخ شروع | تاریخ پایان | ساعت شروع | ساعت پایان | شهریه (ریال) | ثبت نام |
---|---|---|---|---|---|---|
حضوری | 1400-02-04 | 1400-02-06 | 8:30 | 16:30 | 18,000,000 | ثبت نام |
حضوری | 1400-04-12 | 1400-04-14 | 8:30 | 16:30 | 18,000,000 | ثبت نام |
محتوای دوره بازرسي سازه های فولادی مطابق با کد AWS D1.1 و مقررات ملی ساختمان
- متغيرهاي اساسي- غير اساسي و اساسي مشروط در فرآيندهاي مختلف جوشكاري
- اصول و کاربرد فرآيندهاي جوشكاري (FCAW,SAW,GTAW,GMAW,SMAW)
- الزامات انواع اتصالات جوشي مجاز در سازه های فولادی
- الزامات مواد اولیه و انواع مواد مصرفي جوش از قبيل الكترود، سيم جوش و پودر در سازه های فولادی
- الزامات پيش گرم و عمليات حرارتي پس از جوشكاري برای سازه های فولادی
- الزامات شرایط جوی سایت در جوشکاری سازه های فولادی
- الزامات وضعيتهاي جوشكاري ،مشخصات الكتريكي؛ آمپر، ولت و قطبيت ، تكنيكهاي جوشكاري
- آزمايشات مورد نياز در تاييد دستور العمل جوشكاري و پرسنل جوشكار
- محدودههاي پذيرش ( Range Qualified )
- تأييد صلاحيت جوشكاران و اپراتورهاي جوشكاري در سازه های فولادی
- کنترل ابعادی در سازه های فولادی
- الزامات بازرسی چشمی جوش و محدوده پذیرش ناپیوستگی ها در سازه های فولادی
- الزامات تایید صلاحیت بازرسین جوش و اپراتور های NDT
- الزامات تست های غیر مخربUT,PT,MT
- آشنایی با مباحث 10و11 مقررات ملی ساختمان و آیین نامه جوشکاری ساختمانی ایران نشریه شماره 228
- رفع اشكال، مرور مباحث گذشته و آزمون
مخاطبین دوره بازرسي سازه های فولادی مطابق با کد AWS D1.1 و مقررات ملی ساختمان
تکنیسینها و مهندسین واحدهای تولیدی ، بازرسی فنی و کنترل کیفیت (QC ) ، واحدهای تعمیرات ، واحد های مهندسی جوش ،کارشناسان دستگاه نظارت ، دانشجویان و کلیه افراد علاقمند و مرتبط با بازرسی فنی سازه های فولادی جوشکاری شده
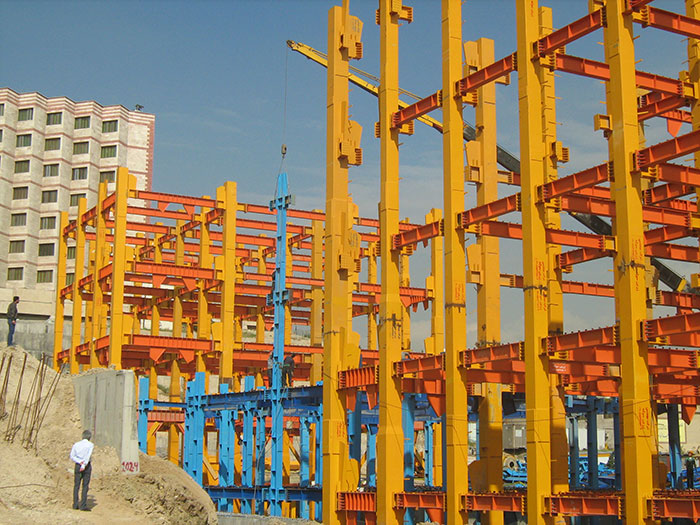
توانمندی ها پس از طی دوره بازرسي سازه های فولادی مطابق با کد AWS D1.1 و مقررات ملی ساختمان در شرکت آریا آزمون صنعت
- کنترل مدارک دستور العمل های جوشکاری (WPS) و آگاهی از انواع آزمایشات مورد نیاز برای تایید WPS
- انتخاب پروسه جوشکاری و الکترود مناسب با توجه به جنس و مشخصات قطعه
- توانایی تهیه مدارک تایید دستورالعمل جوشکاری (PQR)
- آگاهی از الزامات بازرسی جوش ها در سازه های فولادی
- بازبینی و بررسی صحت مدارک WPS,PQR در پروژه های سازه فولادی
- توانایی کافی نسبت به عملیات بازرسی روی سازه های فولادی شامل کنترل مواد پایه ، الکترود ها ، WPS,PQR ، تاییدصلاحیت جوشکاران ، کنترل ابعادی سازه و نیز سایر الزامات بازرسی روی سازه های فولادی طبق AWS D1.1
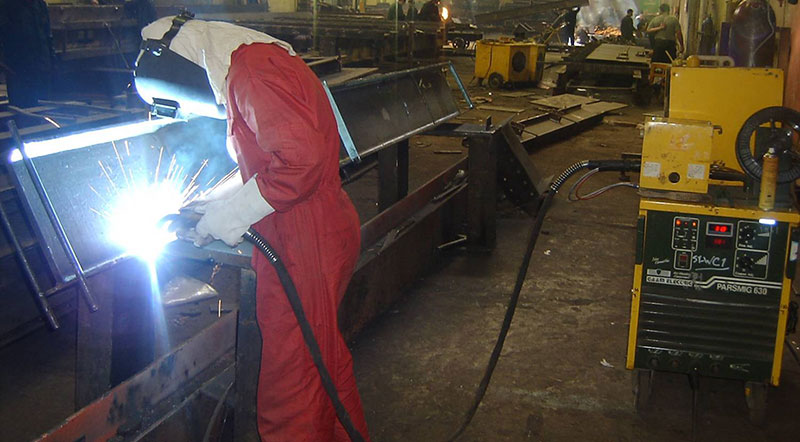
گواهینامه های قابل صدور پس از طی دوره بازرسي سازه های فولادی مطابق با کد AWS D1.1
- گواهینامه معتبر پایان دوره از طرف موسسه آریا آزمون صنعت مورد تایید سازمان های فوق
- امکان صدور گواهینامه از طرف سازمان آموزش فنی و حرفه ای کشور
مزایای دوره بازرسي سازه های فولادی مطابق با کد AWS D1.1 برای افرادی که قصد مهاجرت دارند
گواهینامه دوره بازرسي سازه های فولادی موسسه آریا آزمون صنعت با توجه به اعتبارات سازمانی این موسسه و اینکه دوره بر اساس الزامات استاندارد معتبر AWS D1.1 برگزار می شود ، نیاز به ترجمه نداشته و مستقیما در بسیاری از کشورهای جهان، معتبر و قابل استفاده می باشد. لذا بسیاری از افرادی که قصد مهاجرت به کشور های مختلف را دارند به منظور کسب دانش فنی و مهارت در حوزه بازرسی فنی سازه های فولادی و نیز اخذ یک گواهینامه معتبر، به موسسه آریا آزمون صنعت مراجعه می کنند.
ضمنا مدارکی که فرد پیرو گذراندن دوره در این موسسه، از سازمان آموزش فنی و حرفه ای کشور دریافت میکند، پس ازترجمه و با توجه به دولتی بودن سازمان فنی و حرفه ای، بسیار معتبر بوده و به عنوان یک مدرک قابل ارایه در پروسه مهاجرت استفاده می شود.
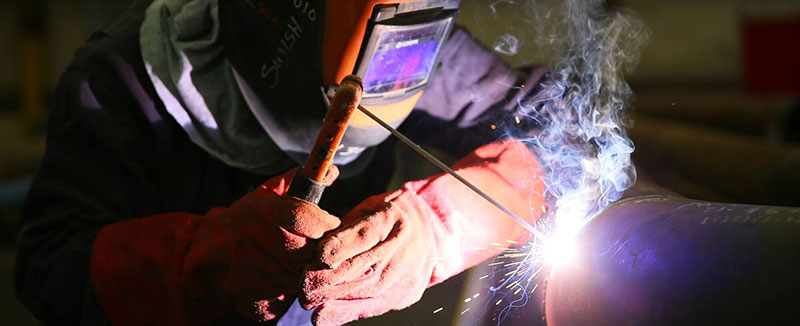
آشنایی با بازرسی جوش در ساخت سازه های فولادی مطابق استاندارد AWS D1.1 و آیین نامه جوشکاری ساختمانی ایران ( نشریه 228 )
جوشکاری يک فرآیندی ویژه است . نظارت بر مراحل مختلف جوشکاری، برشکاری و آماده سازی می تواند از احتمال بروز عیوب تا حد بسیار بالایی بکاهد و از تلفات مالی و جانی در آینده جلوگیری نماید.
دستگاه نظارت باید در زمینه بازرسی جوش و آزمايشهاي غيرمخرب (NDT) از شرکتهای دارای افراد تایید شده استفاده نماید. آموزش جز لاینفک جهت تایید صلاحیت کاری پرسنل مرتبط با جوش (بازرس ، جوشکار و پرسنل NDT)است. عمده ترین عامل از بین رفتن سازه ها در حوادثی مانند زلزله به علت نبودن نظارت کافی در حین ساخت و یا عدم مهارت کافی در پرسنل اجرایی اعم از جوشکاران و بازرسین جوش است.
آیا کیفیت سازه فولادی ضامن سلامت شما در برابر زلزله خواهد بود؟
- آيا اسکلت فلزی ساختمان شما ضامن زنده ماندن شما در زلزله خواهد بود؟
- آيا اسكلت فلزي ساختمان شما مستحكم است؟
- آيا جوشكار سازه فلزی ساختمان شما بر اساس استانداردآموزش ديده و تاييد صلاحيت شده است؟
- آيا تجهيزات جوشكاري شما مطابق استاندارد بوده است؟
- آيا مواد مصرفی بکار رفته در جوشكاري ساختمان شما مطابق استاندارد است؟
- آيا ساختمان شما بازرس جوش آموزش ديده و تاييد صلاحيت شده داشته است؟
- آيا تست جوش بر روي ساختمان شما از طريق شرکتهای دارای صلاحيت و مطابق استاندارد انجام شده است؟
- آيا به نظر شما جوش غير استاندارد مقاوم در برابر زلزله خواهند بود؟
- آيا اسكلت فلزي ساختمان شما بر اساس استاندارد جوشكاري شده است؟
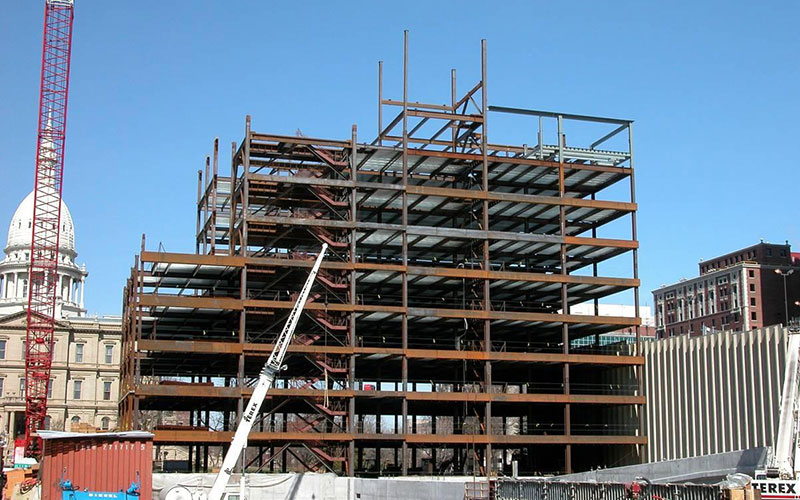
در سطح جهانی، قدمت استفاده از جوش در ساخت اسکلتهاي فولادی شاید به 100سال برسد. در کشور ما نیز شاید بتوان قدمتي 50 ساله برای جوشکاری در ساختمان تصور نمود. طی این سالیان نسبتا طولانی، مسلما پیشرفت های قابل توجهی در شناخت جوش و توسعه فناوری مربوطه صورت گرفته است.
رعايت اصول ايمنی جوش در ساخت سازه های فلزی از آن جهت برای ما بسيار با اهميت است که از نظر موقعيت جغرافيائی ايران در خط زلزله واقع شده و می طلبد که نظارت دقيقتر و بيشتری اعمال گردد . دقيقا کاری که ژاپنی ها سالها قبل با برنامه ريزی دقيق انجام داده و ثمره آنرا امروزه می بينيم که حتی در زلزله های بالاتر از 7.5 ريشتر هيچ آسيبی به ساختمانها و مهمتر از آن به شهروندان وارد نمی گردد. اما در ايران می بينيم که بسادگی در زمين لرزه هائی با شدت خيلی کمتر از آنچه در ژاپن اتفاق افتاده هزاران تن از هموطنان بی گناه در زير آوار از بين می روند ، نمونه ملموس آن منجيل ، بم می باشد .حال بايستی از اين اتفاقات درس گرفته و دنبال راه چاره ای باشيم . تنها راه و چاره اينست که با در پيش گرفتن رويه ای صحيح و استاندارد ، عوامل دخيل در توليد را از نظر علمی ارتقاء داده و نيز مراحل ساخت را دقيقا نظارت و اجرا کنيم .
شناسائی علل تخريب سازه های اسکلت فلزی
اگر از تعداد پروژه های عمرانی خاص صرفنظر کنیم ، غالبا اکثر پرسنل جوشکاری شاغل در بخش ساختمان، آموزش لازم ندیده، و فاقد تبحر لازم هستند و معضل مهمتر اینکه هیچ کنترلی بر روی کیفیت اجرای جوش وجود ندارد. در ميان روشهاي مختلف توليد، تكنولوژي جوشكاري به دليل ويژگيهاي خاص و تنوع در فرآيندهاي آن جايگاه متمایزی را به خود اختصاص داده و اتصالاتي كه توسط جوشكاري ايجاد ميشوند از نظر ارزيابيهاي كيفي قابل قياس با ساير روشهاي اتصال نميباشند. به همين دليل در صنعت، از جوشكاري به عنوان فرآيند خاص (Special Process) ياد شده است. بر طبق استاندارد ISO 9001 فرآيند خاص به فرآيندي گفته ميشود كه نتوان نتیجه کیفی آن را بطور کامل از طریق بازرسی و آزمایشهای نهایی محصول مورد تصدیق قرار داد خصوصاً در مواردی که نارسایی محصول فقط پس از مصرف آن ظاهر میگردد. پر واضح است که صرفاً از طریق بازرسی نهایی محصول، حتی با دقیقترین روشهای NDT، نمیتوان کیفیت محصول را تضمین کرده و یا بهبود داد، بلکه برای اطمینان از سلامت محصول در حین بهرهبرداری، ضروری است در مراحل قبل و حین ساخت نیز کلیه پارامترهای تأثیرگذار بر فرآیند شامل صلاحیت پرسنل، تجهیزات، تهیه و اجرای دستورالعملها، مواد مصرفی، نحوه بازرسی و آزمونها و ... به طور کامل تحت پایش و نظارت قرار گیرد.
بازرسی قبل از عمليات جوشکاری
- کنترل تهیه دستور العمل هاي جوشکاری WPS
- كنترل روند تاییدیه رويه جوشکاری PQR
- آزمون جوشکاران، صدور گواهینامه، انتخاب جوشکاران
- ارزیابی کیفیت فلز پایه و مواد مصرفی جوش
- ارزیابی دستگاههای جوش و برش
- کنترل طرح اتصال و آماده سازی قطعات مطابق نقشه در کارگاه
- کنترل صلاحیت بازرسین جوش و اپراتور های NDT
بازرس بايستی دانش و اصول اطلاعات مربوط به كنترل دستورالعمل های جوش ، روشهای آزمون لازم در مورد مقاطع جوشی ، استانداردها ، نقشه خوانی و ... داشته باشد. وظيفه بازرس، راهبری و نظارت بر سازه جوشی طبق اصول و روشهای مناسب می باشد.
اصولا بازرس جوش طبق استاندارد AWS QC1 آموزش ديده و تاييد صلاحيت می شود . پرسنل NDT بايستی مطابق رويه مکتوب SNT-TC1-A آموزش ديده و دارای Level های بازرسی معتبر ( Level II )در زمينه تست های غير مخرب (NDT) که شامل PT,UT,RT,MT,ET و ... است، باشند.
خصوصيات و يا صلاحيت های بازرس جوش
- بازرس جوش بايد خوش برخورد بوده و خصوصيات فيزيکی و قدرت بينايی مناسب داشته باشد .
- بازرسين جوش بايستی با نقشه های مهندسی آشنايی کامل داشته و نقشه را خوب خوانده و تشريح کنند .
- آشنايی کامل با اصطلاحات تعريف شده بين المللی ، علائم جوشکاری و کدهای استاندارد.
- دوره های کافی در رابطه با آزمونهای غير مخرب ديده باشند و دارای مدارک معتبر NDT باشند .
- توانايی آزمايش تاييد صلاحيت جوشکاری را بر اساس کدها و استانداردها داشته باشند .
- اطلاعات کافی از متالورژی جوش و تکنولوژی جوش داشته باشند ، تا در هنگام ضرورت قادر به تجزيه و تحليل مسائل مهندسی جوش باشند .
- سابقه بازرسی جوش داشته ، عيوب جوش را به طور کامل بشناسند و روش های پيشگيری و رفع آنها را بدانند .
- از فرآيندهای جوشکاری اطلاعات کافی داشته باشند .
- گزارشات کنترل کيفيت را در مراحل مختلف ساخت ، تهيه و تثبيت نمايند .
- در تمامی مراحل ساخت پروژه ، حضور داشته باشند .
وظايف بازرس جوش
- تفسير نقشه های جوشکاری و مشخصات آنها .
- بررسی سفارش خريد به منظور حصول اطمينان از دسترسی تعيين مواد جوشکاری و مواد مصرفی
- بررسی و شناسايی مواد دريافت شده طبق مشخصات سفارش خريد .
- بررسی ترکيبات شيميايی و خواص مکانيکی از روی گزارش بورد طبق نيازمنديهای معين شده .
- بررسی فلز مبنا از نظر عيوب و انحرافات مجاز .(آزمايش عدم تورق )
- بررسی نحوه انبار کردن فلز پر کننده (الکترودها ) و ديگر مواد مصرفی .
- بررسی تجهيزات مورد استفاده (جوش و برش ).
- بررسی آماده سازی اتصال جوش .
- بررسی جفت و جوری و اتصال يا مونتاژ قطعات .
- بررسی به کار گرفتن دستورالعملهای جوشکاری تاييد شده (WPS)
- بررسی ارزيابی صلاحيت جوشکاران و اپراتورهای جوشکاری .
- انجام آزمايشات غير مخرب بر اساس دستورالعملها و استانداردها .
- ارزيابی نتايج آزمايش .
- نگهداری سوابق .
- تهيه و تنظيم گزارش .
بازرس بایستی تایید کند که :
- تمامی پیمانکاران با مسئولیت های ساخت در زمینه جوشکاری آشنا بوده و آنرا رعایت می کند.
- متد های تضمین کیفیت جهت حصول اطمینان از برقراری الزامات مهندسی و طراحی حین ساخت برقرار می باشد.
- رویه های لازم موجود بوده و صحت کارکرد تجهیزات مستند گردیده است.
- پیمانکار رویه هایی برای حصول اطمینان از کارکرد پرسنل QC و پایش تاثیر گذاری آنها دارد.
- جوشکاری فولاد ساختمانی تحت شرایط کنترل شده انجام می گیرد.
- بازرس باید تایید کند که مهارت کلیه پرسنل مرتبط با جوش تایید شده و در سطح مرتبط با فعالیت انجام گرفته می باشد.
جوشکاران و اپراتورهای جوش و خال جوش کاران که در محدوده فرآیندهای مورد تایید AWS D1.1 فعالیت می کنند باید براساس آزمون های ذکر شده در AWS D1.1 مورد ارزیابی قرار گیرند. جوشکارانی که در یک محدوده 6 ماهه پس از صدور گواهینامه خویش در همان محدوده تایید شده فعالیتی نداشته باشند باید مورد ارزیابی مجدد قرار گیرند.( AWS D1.1)
تمامی جوشکاران بايستی قبل از جوشکاری بر روی سازه فلزی توسط بازرس تعيين صلاحيت شوند . بازرس بايستی متناسب با نوع نياز و روش و الکترود و نحوه اتصالات جوش در سازه از جوشکاران بر اساس استاندارد آزمايش بعمل آورد و پس از تاييد ، متناسب با نوع تاييد و گواهی که هر جوشکار دريافت می کند بايستی در پروژه از وی استفاده شود . جوشکارانی که کيفيت جوش آنها تاييد نشده است نمی توانند جوشکاری نمايند . معمولاً در صورت تست در حالت گوشه علاوه بر کنترل چشمی ظاهر جوش ، آزمايش شکست نمونه جوش گوشه انجام می شود و در صورت جوشکاری در حالت نفوذی و اتصال لب به لب علاوه بر کنترل چشمی آزمايش خمش و يا آزمايش غير مخرب UT با RT انجام می شود .
بازرسی حين جوشکاری
- تطيبق اينکه کار مطابق نقشه اجرایی و مشخصات سازه می باشد
- تطابق کار در حال اجرا با رویه های تایید شده جوشكاري
- استفاده از پرسنل و جوشکاران تایید شده برای محدوده مشخص
- كنترل آماده سازي قطعات بر اساس نقشه ها و WPS
- کنترل توالي اجراي جوش براي اجتناب از تابيدگي قطعات
- كنترل عمليات تميزكاري بين پاس ها
بازرسی پس از عمليات جوشکاری
- بازرسی چشمي نهایی و آزمون های NDT مورد لزوم
- كنترل ابعادي جوش ها و اجزاي سازه بر اساس نقشه
- ثبت کلیه عملیات انجام شده و تهیه شناسنامه هر قطعه به اتمام رسیده طبق استاندارد
بازرسی چشمی (Visual Inspection )
يکی از ساده ترين و سريع ترين و کم خرج ترين روش برای کشف بعضی عيوب نظير موارد زير ، بازرسی چشمی می باشد که اين آزمايش غالباً با دقت و با کمک انواع ذره بين با درشت نمايی 5-20 مرتبه انجام می گيرد .سطح جوش گوشه تا مقدار محدودی می تواند محدب يا مقعر باشد به استثنای عيوب مربوط به بريدگی پای جوش وجود ساير عيوب در دو انتهای جوش های منقطع ، خارج از طول موثر جوش مهم نمی باشد . جوش های شياری ترجيحاٌ بايد با حداقل تحدب اجرا شوند . در درزهای لب به لب يا اتصالات گونيا حداکثر تحدب برابر با 3 ميليمتر می باشد و بايد داری انتقال تدريجی با سطح فلز پايه باشد . عيوبی که می توان با بازرسی چشمی تشخيص داد عبارتند از :
- خلل و فرج هايی که به سطح جوش رسيده باشند .
- سوختگی و بريدگی کناره جوش و يا پر نشدن کامل درز جوش
- حفره انتهايی جوش همراه با سوراخ ناشی از انقباض حاصل از انجماد
- گرده جوش اضافی و يا سر رفتن فلز جوش
- موج های زياد و مهره های ناموزون و خشن سطح جوش
- پاشش جوش ، جرقه و ترشح و يا لکه قوس
- ترکيدگی ها در جوش يا منطقه مجاور جوش که قابل تشخيص با چشم و يا به کمک ذره بين باشند
- جا بجا شدن ، تاب برداشتن و تغییر ابعاد اجزاء مورد جوش
بازرسی به کمک مايعات نافذ (PT)
بازرسی به کمک مواد نافذ از شيوه های غير مخرب برای محل يابی معايب سطحی می باشد . اين آزمايش برای فلزات غير مغناطيسی نظير فولاد زنگ نزن ، آلومينيوم ، منيزيم ، تنگستن و پلاستيک ها نيز قابل کارکرد است . آزمايش با مواد نافذ جهت تشخيص عيوب داخلی قابل استفاده نمی باشد . سطح مورد بازرسی بايد در ابتدا از لکه های روغن ، گريس و مواد ناخالص خارجی تميز شود . سپس ماده رنگی مورد نظر بر روی سطح پاشيده و در داخل ترک ها و ساير ناهمواری ها نفوذ می کند . رنگ اضافی از رو سطح پاک شده و سپس يک مايع فوق العاده فرار حاوی ذرات ريز سفيد رنگ بر روی سطح پاشيده می شود . اين ماده بنام ماده ظهور (ظاهر کننده ) خوانده می شود .تبخير مايع فرار باعث بر جای ماندن گرد خشک سفيد رنگ بر روی ماده قرمز رنگ نفوذ کرده در ترک ها می گردد و بر اثر عمل مويينگی ، ماده قرمز از ترک بيرون کشيده شده و پودر سفيد کاملاً قرمز می شود . به همين جهت ترک مورد نظر به وضوح با اين روش قابل شناسايی است .
مزايای روش (PT) :
- ساده بودن روش کار.
- بسيار ارزان است.
- بازرسی با مايع نافذ برای کليه قطعات به هر شکل و هر اندازه قابل استفاده است .
- قطعات در حال کار را می توان در محل کار بازرسی کرد.
معايب روش (PT) :
- فقط برای عيوب سطحی بکار ميرود .
- برای قطعاتی که دارای سطوح زبر و خشن هستند ، استفاده نمی شود .
عيوبی که می توان با بازرسی مايعات نافذ تشخيص داد عبارتند از :
- ترکهايی که به سطح قطعه رسيده باشند
- حفرات سطحی
- ذوب ناقص و يا عدم امتزاجهای سطحی
بازرسی با ذرات مغناطيسی (Magnetic Particle Inspection) :
بازرسی با ذرات معناطيسی يکی از روش های ساده و سريع برای آشکار کردن بعضی عيوب سطحی غير قابل رويت و يا کمی زير سطح نظير ترک های خيلی ريز ، ذرات سرباره محبوس نشده و خلل و فرج که در عمق زيادی قرار نداشته باشند ، است . در اين روش از يک جريان قوی ايجاد کننده حوزه مغناطيسی در جوش استفاده می شود که پس از پاشيدن پودر ريز مغناطيسی شونده بر روی منطقه جوش ، اگر عيوبی در سطح يا لايه زير سطح وجود داشته باشد موجب قطع نيرو و خطوط مغناطيس شده و منجر به تمرکز ذرات پودر در اطراف عيب می شود (يجاد قطب های مغناطيسی در دو طرف عيب ) . به اين ترتيب اندازه ، شکل و موقعيت عيب مشخص می شود . طبيعی است که هر چه عيب در عمق پايين تری باشد نياز به حوزه مغناطيسی قوی تر بوده و اين تمرکز ذرات در سطح نا مشخص تر است .
مزايای روش ذرات مغناطيسی :
- عيوب سطحی و زير سطحی تا عمق حداکثر 7 ميليمتر را می توان بازرسی نمود.
- اغلب ضروری نيست که سطح قطعه با دقت تميز کاری شود.
- با اين روش می توان تقريباً پهنای عيب را حدس زد.
- ارزان قيمت است.
معايب روش ذرات مغناطيسی :
- فقط برای مواد فرومانتيک قابل استفاده است.
- هميشه بهتر است که ميدان مغناطيسی عمود بر يوب باشد.
- بعضی مواقع لازم است يک قطعه را چندين بار مغناطيسی کنيم.
- بعد از عمل بازرسی بايد مغناطيس زدايی انجام گيرد.
- مهارت و تجربه زيادی نياز دارد.
- برای تشخيص عيوب سطحی و نزديک به سطح کاربرد دارد.
عيوبی که می توان با بازرسی ذرات مغناطيسی تشخيص داد عبارتند از :
- ترکهای سطحی و زير سطحی
- خلل و فرج و پروسيتی های سطحی و نزديک به سطح
آزمايش با امواج فراصوتی (Ultrasonic Testing) :
در اين آزمايش ارتعاشات يا امواج فرکانس بالا برای تشخيص موقعيت و اندازه عيوب سطحی و عمق نظير خلل و فرج ، ترک ، سرباره محبوس شده ، نفوذ ناقص و حتی ضخامت جوش يا قطعه کار بکار می رود . اين روش که بسيار حساس و دقيق است برای فلزات آهنی و غير آهنی و حتی غير فلزات (سراميک و پلاستيک ) نيز قابل استفاده و دارای کاربرد می باشد . اصول کلی روش بدين ترتيب است که از عبور جريان الکتريکی متناوب با فرکانس بالا (يک ميليون سيکل در ثانيه ) از کريستال کوارتز ، انرژی الکتريکی به انرزی مکانيکی تبديل می شود . در قسمت اول سيکل سطح کريستال منبسط شده و در نيم سيکل ديگر منقبض می شود و بدين ترتيب ارتعاش مکانيکی ايجاد می شود . اگر سطح صاف شده مورد آزمايش با اين سطح منتشر کننده موج تماس حاصل نمايد امواج به طور موثر از Probe به کار منتقل می شود . اگر کوچکترين عيبی در مسير اين امواج باشد ، تمام يا قسمتی از موج در برخورد با اين عيب ، منعکس می شود و در روی صفحه کاملاً مشهود خواهد بود . اگر منحنی استانداردی که نشان دهنده فاصله يا زمان رفت و برگشت موج است در روی صفحه موجود باشد ، به راحتی می توان فاصله عيب را تا سطح نيز تعيين کرد .
مزايای روش Ultrasonic Testing :
- با استفاده از اين روش زير سطح و داخل جوش و عمق ريشه شيار قابل شناسايی می باشد .
- قابل انتقال در هر موقعيت سازه جهت تست می باشد .
- دقت کار بالا است .
- نوع ، ابعاد و موقعيت عيب قابل شناسايی است .
معايب روش Ultrasonic Testing :
- گران بودن تجهيزات و دستگاه .
- مهارت اپراتور بايد زياد باشد و نياز به آموزش های خاص دارد .
- تميز بودن و صاف بودن سطح محل آزمايش مهم است و در دقت کار اثر دارد .(بايستی محل آزمايش سنگ زده شود و از گريس يا روغن برای پر کردن ناهمواری ها و انتقال امواج صوتی استفاده شود .)
- عيوبی که در راستای جهت انتشار امواج هستند با اين روش به خوبی آشکار نمی شوند .
عيوبی که می توان با بازرسی التراسونيک تشخيص داد عبارتند از :
- خلل و فرج
- ترک
- سرباره محبوس شده
- نفوذ ناقص و ذوب ناقص
- خوردگی کنار جوش (ريشه undercut )
- ضخامت جوش يا قطعه کار
راديو گرافی (Radiographic Inspection) :
پرتونگاری يکی از روش های آزمايش غير مخرب می باشد که نوع و محل عيوب داخلی و بسيار ريز جوش را نشان می دهد . در اين روش از دو نوع پرتو X و گاما استفاده می شود. اشعه گاما به خاطر طول موج کوتاه خود می تواند در ضخامت های نسبتاً زيادی از مواد نفوذ کند. در آزمايش پرتونگاری يک عکس از وضعيت داخلی فلز جوش گرفته می شود . در حين عکس برداری ، فيلم در يک طرف و منبع پرتوزا (X يا گاما) در سمت ديگر قطعه قرار می گيرد . پرتو راديويی در ضخامت فلز نفوذ کرده و پس از عبور از اين ضخامت لکه ای بر روی صفحه فيلم ايجاد می کند . ميزان جذب پرتوهای راديويی توسط مواد مختلف متفاوت است . گل جوش ، حفره گازی ، ترک ها، بريدگی های کنار جوش و قسمت های نفوذ ناقص جوش ، تراکم کمتری نسبت به فولاد سالم دارند . بنابراين در حوالی اين قسمت ها پرتو بيشتری به سطح فيلم می رسد و عيوب فلز جوش ، به صورت لکه های تاريکی بر روی فيلم ثبت می شوند . اين شيوه پرتونگاری حضور معايب مختلف در فلز جوش و فلز پايه را مسجل کرده و اندازه ، شکل و محل آنها را ثبت می کند .
مزايای راديوگرافی(Radiographic Inspection) :
- برای بررسی عيوب عمقی موثر و مفيد است .
- مواد فلزی آهنی و غير فلزی را می توان راديوگرافی کرد .
- محل عيوب و شکل ظاهری عيب را می توان در فيلم راديوگرافی ملاحظه نمود .
- . مستند سازی به صورت فيلم راديوگراف
معايب راديو گرافی(Radiographic Inspection) :
- گران بودن ابزار و وسايل کار
- نياز به اتاق تاريک برای ظهور و ثبوت فيلم
- تنظيم دستگاه و تجهيزات زمان بر است
- با تجهیزات پرتابل داخل کشور حداکثر 75 ميليمتر از عمق فولاد را می توان به طور موثر راديوگرافی کرد .
- خطرات اشعه راديو اکتيو است .
- عيوبی که عمود بر جهت انتشار امواج هستند با اين روش به خوبی آشکار نمی شوند مانند Lamination
عيوبی که می توان با بازرسی راديوگرافی تشخيص داد عبارتند از :
- خلل و فرج
- ترک
- سرباره محبوس شده
- نفوذ ناقص و ذوب ناقص
- خوردگی کنار جوش
- کاهش ضخامت جوش يا قطعه کار
محدوده پذيرش عيوب در بازرسي چشمي جوش مطابق با AWS D1.1
نوع ناپيوستگي و محدودة پذيرش | كاربرد | ||||
---|---|---|---|---|---|
(1) ممنوعيت وجود ترك (Crack Prohibition)
هرگونه ترك غيرقابل پذيرش ميباشد مستقل از سايز و محل قرارگيري آن
|
○
△
□
|
||||
(2) ذوب بين فلز جوش و فلز پايه (Weld/Base-Metal Fusion)
بايستي ذوب كامل بين لايههاي جوش و همچنين بين فلز جوش و فلز پايه وجود داشته باشد.
|
○
△
□
|
||||
(3) مقطع چاله جوش (Crater Cross Section)
تمامي چالههاي جوش بايد تا اندازه معين پر شوند، غير از چالههايي كه در انتهاي جوشهاي نبشي منقطع خارج از طول مؤثر جوش قرار دارند.
|
○
△
□
|
||||
(4) پروفيل جوش (Weld Profile)
پروفيل جوشها بايد مطابق با بند 5.24 مورد ارزيابي قرار گيرد.
|
○
△
□
|
||||
(5) زمان بازرسي (Time of Inspection)
بازرسي چشمي جوش براي تمام انواع فولادها، بلافاصله پس از اتمام جوشكاري و رسيدن به دماي محيط قابل اجراء ميباشد. استثناً در فولادهاي A514 ، A517 ، A709 گريد 100 و 100W ، عمليات بازرسي چشمي بايد حداقل 48 ساعت پس از تكميل جوش انجام شود.
|
○
△
□
|
||||
(6) كاهش سايز جوش (Undersized Weld)
كوچك بودن سايز جوشهاي نبشي نسبت به سايز اسمي، در صورتيكه مقدارش از جدول زير تبعيت كند، قابل قبول بوده و نيازي به تعمير ندارد (منظور از سايز، ساق جوش ميباشد).
در هيچ حالتي نبايد كاهش سايز، در طولي فراتر از 10% طول كلي جوش تكرار شود. در اتصالات جوشي بال به جان در تيرها، هيچ كاهش سايزي در دو انتهاي تيرآهن در فاصلهاي معادل دو برابر پهناي بال، مجاز نميباشد.
|
○
△
□
|
||||
(7) سوختگي كنار جوش (Undercut)
(A) براي قطعاتي با ضخامت كمتر از 25mm ، عمق سوختگي كنار جوش نبايد از 1mm تجاوز نمايد. البته به شرطي كه مجموع طول اين عيب در هر 300mm خط جوش از 50mm تجاوز نكند، عمق آن حداكثر تا 2mm ، مجاز خواهد بود. براي ضخامتهاي بزرگتر يا مساوي 25mm ، حداكثر عمق مجاز سوختگي كناره، براي هر طولي از جوش، 2mm ميباشد.
|
○
|
||||
(B) در اعضاي اصلي سازه، هنگامي كه جهت تنش كششي عمود بر راستاي جوش است، سوختگي كناره حداكثر تا عمق 0.25mm مجاز ميباشد. براي تمامي حالتهاي ديگر، عمق اين عيب نبايد از 1mm تجاوز نمايد. |
△
□
|
||||
(8) حفرات گازي (Porosity)
(A) در اتصالات سر به سر با جوشهاي شياري نفوذ كامل، در صورتيكه راستاي جوش عمود بر جهت تنش كششي باشد، هيچ حفرة گازي لولهاي شكل (Piping Porosity) مجاز نميباشد.
براي ساير جوشهاي شياري و جوشهاي نبشي، مجموع قطر حفرات لولهاي قابل روئت با قطر 1mm يا بيشتر، نبايد از 10mm در هر 25mm طول جوش و از 20mm در هر 300mm طول جوش، تجاوز نمايد.
|
○
|
||||
(B) تعداد حفرات گازي لولهاي شكل در جوشهاي نبشي نبايد بيشتر از يك عدد در هر 100mm طول جوش باشد و حداكثر قطر آن نبايد از 2.5mm تجاوز نمايد. استثناً براي جوشهاي نبشي اجرا شده بين تقويتكنندهها (Stiffeners) و جان تير آهن، مجموع قطر حفرات لولهاي نبايد از 10mm در هر 25mm طول جوش و از 20mm در هر 300mm طول جوش تجاوز نمايد. |
△
□
|
||||
(C) در اتصالات سر به سر با جوشهاي شياري نفوذ كامل، در صورتيكه راستاي جوش عمود بر جهت تنش كششي باشد، هيچ حفره گازي لولهاي مجاز نميباشد. براي ساير جوشهاي شياري، تعداد حفرات گازي لولهاي نبايد بيشتر از يك عدد در هر 100mm طول جوش بوده و حداكثر قطر آن نبايد از 2.5mm تجاوز نمايد. |
△
□
|
||||
○ : بارگذاري استاتيكي در اتصالات غيرمحيطي
△ : بارگذاري سيكلي در اتصالات غيرمحيطي
□ : اتصالات محيطي (تحت هر نوع بارگذاري)
|