بازرسی حین ساخت و نصب مخازن ذخیره مطابق با API 650
ثبت نام دوره
نوع دوره | تاریخ شروع | تاریخ پایان | ساعت شروع | ساعت پایان | شهریه (ریال) | ثبت نام |
---|---|---|---|---|---|---|
حضوری | 1400-02-18 | 1400-02-20 | 8:30 | 16:30 | 18,000,000 | ثبت نام |
حضوری | 1400-05-02 | 1400-05-04 | 8:30 | 16:30 | 18,000,000 | ثبت نام |
مدت دوره: 3 روز
محتوای دوره:
- مقدمه و آشنایی کلی با مخزن ذخیره و مراجع مورد استفاده
- انتخاب متریال در مخازن ذخیره و گروه بندی متریال بر استانداردهای API 650,API620
- محاسبه ضخامت برای بخش های مختلف مخزن،بدنه،کف،سقف و متعلقات و الزامات مربوط به نازل ها
- ساخت و نصب مخازن
- آزمون های مورد نیاز مانند هیدروتست و سایر آزمون های غیرمخرب
- مارکینگ و سایر موارد
- الزامات تکمیلی برای ساخت مخازن بر اساس ضمیمه های API 650
مخاطبین دوره:
تکنیسینها و مهندسین واحدهای بازرسی فنی و کنترل کیفیت (QC ) ، واحدهای تعمیرات ، کارشناسان دستگاه نظارت که در بازرسي مخازن ذخیره در ساخت و نصب در صنايع نفت ، گاز ، پتروشيمي ، پالايشگاهي و نيروگاهي فعاليت دارند ، دانشجویان و کلیه افراد علاقمند و مرتبط با بازرسی مخازن ذخیره
توانمندیها پس از طی دوره:
شرکت کنندگان در دوره مذکور نسبت به اصول بازرسی مخازن ذخیره در دوره ساخت و نصب بر اساس استاندارد API 650 آشنایی کافی کسب خواهند نمود .
گواهینامه:
به قبول شدگان در آزمونهای نهایی گواهینامه معتب API 650 In-service Storage Tank Inspection اعطا خواهد شد.
پیش نیاز دوره:
آشنایی با اصول بازرسی جوش و آزمایشات غیرمخرب (NDT ) روی مخازن ذخیره و دارا بودن سابقه کار مرتبط و توانایی خواندن و درک متون انگلیسی مرتبط .
آشنایی با بازرسي حین ساخت و نصب مخازن ذخیره
مقدمه
کلیه سازه های صنعتی از جمله مخازن ذخیره بايستی مطابق با دستورالعمل ارائه شده توسط کارفرما ساخته و بازرسی شوند. در بسیاری از موارد حدود مجاز جهت بازرسی مخازن ذخیره اتمسفریک که بالاتر از سطح زمین ساخته می شوند بر اساس استاندارد API Std. 650 که در اين مجال به آن پرداخته می شود ، می باشد. ساخت مخزن بايد مطابق با الزامات بيان شده و نقشه هاي ساخت باشد . اگر هرگونه تعارضي بين مشخصات و نقشه ها موجود باشد وظیفه بازرس است که اين امر را به کارفرما گزارش داده و با مشورت با واحد طراحی این مشکلات حل شود.
کليه متريال و تجهيزات ارسال شده به سايت بايد به دقت از لحاظ کميت , اندازه و مشخصات با نقشه ها و اسناد ارسالي چک شده و مطابق با دستورالعمل ناظر کارفرما انبار شوند. حمل ونقل متريال و تجهيزات بايد به دقت انجام شده تا آسيبي به آنها نرسد . کليه متريال , تجهيزات و جيگها که جهت ساخت استفاده مي شوند بايد قبل از استفاده به دقت چک شوند.
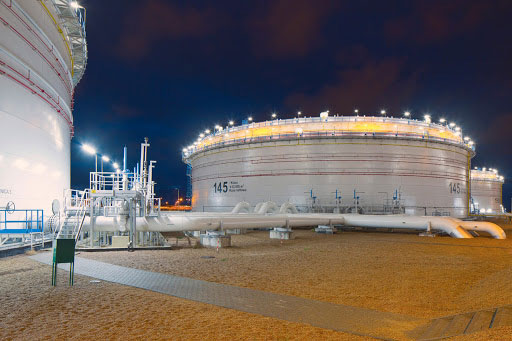
کاربرد مخازن ذخیره
واحدهای پالایشگاهی وپتروشیمی جهت نگهداری مواد اولیه مورد نیاز ، انجام فرایندهای میانی و پایانی و همچنین انبار کردن فرآورده های نفتی گوناگون نیازمند مخازن می باشند . تعداد این مخازن به عواملی چند، چون دوری و نزدیکی واحد به منابع تامین کننده نفت خام ، تعداد و ظرفیت واحدهای پالایش، تنوع فرآورده های تولیدی و سرانجام چگونگی انتقال و پخش فرآورده ها بستگی دارد.
در صنایع شیمیایی ، مواد ارزشمند مانند بنزین یا گاز مایع ، طی فرآیندهای مختلفی از مواد شیمیایی خام، مانند نفت خام جدا می شوند یا از آنها به وجود می آیند. چند راه برای انتقال مواد خام از منابع تامین کننده به واحد فرآیندی وجود دارد که بر حسب مورد و شرایط ، از یکی از آنها مانند خطوط انتقال یا تانکر استفاده می گردد. همچنین محصولات تولیدی نیز به روش های مختلف به بازار داخلی یا خارجی عرضه می شوند.
به دلایل زیادی از جمله یکسان کردن کیفیت محصول، انجام فرایندهای میانی و پایانی ،اندازه گیری حجم محصول جهت فروش، امکان بارگیری و انتقال به تانکر یا کشتی در حداقل زمان ممکن و ... مواد تولیدی را در مخازن یا تانک های مناسب ذخیره نمایند.
به طور کلی مخازن چند وظیفه اصلی به عهده دارند:
1- ذخیره مواد اولیه و خوراک واحدها
2- ذخیره و انجام فرایند میانی و یا نهایی بر روی مواد واسطه تولید شده درفرآیندهای قبلی
3- ذخیره فرآورده ها
4- ذخیره مواد برای بارگیری و پخش
5- همسان نمودن کیفیت محصول
6- معیاری جهت اندازه گیری حجم خوراک و محصول تولید شده
به عنوان مثال مخازن یک پالایشگاه را بنا به نوع کاربرد و منطقه قرارگیری به چهار دسته تقسیم می کنند:
- مخازن نفت خام :
انواع گوناگون نفت خام سبک یا سنگین را می توان به طور جدا یا آمیخته، در این مخازن ذخیره کرد. مخازن امروزی نفت خام، سقفی شناور داشته، بیشتر به لوله های مارپیچ بخار، برای گرم کردن نفت خام در فصل زمستان، پروانه های همزن، عمق سنج و ... مجهزند.
2- مخازن واسطه
این مخازن ، برای دریافت فرآورده های نیم نهایی از یک واحد پالایش، انجام فرایندهای ثانویه و یا تکمیلی و دادن آن ها به واحدهای دیگر برای انجام گرفتن فرآیندهای دیگر پالایش ، یا دریافت ترکیبات گوناگون فرآورده های پیش از آمیختگی و انتقال آن ها به مخازن فرآورده های نهایی به کار برده می شوند.
3- مخازن فرآورده
فرآورده های گوناگون نفتی بنا به مشخصات مورد نظر در این مخازن تهیه و به شبکه پخش انتقال داده می شوند.
4- مخازن بارگیری و پخش
برخی از فرآورده های سبک و سنگین، مانند گاز مایع، روغن موتور، قیر و ... که بردن آن ها به جاهای دوردست از راه خطوط لوله، دشوار یا نشدنی است، در مخازن بارگیری انبار شده، سپس به نفت کش ها یا مخزن دارهای راه آهن منتقل و به محل مصرف فرستاده می گردد. کار بارگیری معمولاً به وسیله تلمبه انجام می گیرد. اگر فرآورده های نفتی روان باشد و فاصله مخزن تا جای بارگیری زیاد نباشد، با ایجاد اختلاف سطح میان مخزن و نقطه بارگیری، مایع با نیروی جاذبه به وسیله نقلیه منتقل می شود. مخازنی که در این سرویس هستند، مخزن های بارگیری و پخش خوانده می شوند.
چون نصب مخازن در هر پالایشگاه، هزینه سرمایه ای بسیار خواهد برد، در طرح پالایشگاه کوشش می گردد تا شمار و ظرفیت مخزن ها به کمترین حد کاهش یابد برای مثال، شمار و ظرفیت مخزن های واسطه تا حد منظور می شود که بتوان تداوم عملیات و موازنه کار عادی دستگاه ها را حفظ کرد. همچنین با انجام عملیات آمیختگی فرآورده های گوناگون در لوله ها و در مرحله انتقال به مخازن، می توان شمار مخزن های واسطه و فرآورده ها را کاهش داد، به شرطی که میان تولید و انتقال فرآورده ها، موازنه برقرار باشد. این کار نیازمند یک برنامه ریزی دقیق روزانه، هفتگی و ماهانه است.
بازرسي ابعادي فونداسيون
شکل ، ارتفاع ، شيب و ترازبودن فونداسيون بايد به دقت بررسي شود تا مدور بودن تانک حفظ شده و فونداسيون آن عاري از تابيدگي و چين خوردگي باشد . به همين دليل فونداسيون بايد نه تنها در شروع ساخت بلکه در مراحل مختلف ساخت نيز چک شود .
مرکز فونداسيون
نقطه مرکزی فوندانسیون بایستی با استفاده از نقاط مرجع موجود در سایت توسط نقشه بردار چک شود تا هیچ گونه انحرافی نسبت به مختصات ارائه شده در نقشه نداشته باشد.
شعاع پد تانک
شعاع پد تانک را بايد توسط متر در چند نقطه چك كرد .مطلب بسیار مهم که در تمام اندازه گیری ها بر روی مخازن باید در نظر گرفت این است که با توجه به این که در مناطق با دمای عمومی بالا مانند عسلویه و بندرعباس تمامی اندازه گیری ها باید در زمان مشخصی از روز انجام شود تا میزان خطا به حداقل خود برسد. همچنین در این مناطق استفاده از دوربین نقشه برداری به جای متر توصیه می گردد.
شيب فونداسيون تانک
فونداسيون تانک بايد مطابق با نقشه هاي ساخت شيب داده شود . در خصوص فوندانسیونها با زیر سازی به صورت سنگ دانه(کراش راک) بهتر است که پیش از ریزش سنگ دانه ها بر روی فوندانسیون شیب لایه زیر را بررسی کرد و پس از ریختن کراش راک و قبل از چیدمان ورقهای کف ، این شیب دوباره کنترل گردد.
تراز كردن فونداسيون
مطابق با استاندارد اختلاف سطح ميان دو نقطه مجاور روي محيط كه به فاصله 10 متر از هم قرار گرفته اند نبايد از3 ± ميلي متر بيشتر باشد . از طرفي اختلاف سطح ميان هر دو نقطه مفروض روي محيط نيز نبايد از 6 ± ميلي متر بيشتر باشد .
علامتگذاري مرکز و جهات
مرکز تانك ونقاط ˚0 , ˚90 , ˚180 و ˚270 در بازرسی و ساخت مخازن بسیار مهم بوده و باید از ابتدا طوری مشخص شوند که تا پایان مراحل ساخت این نقاط قابل شناسایی و ردیابی باشند.
چيدمان ورقهاي انولار و کف
1) در زمان چيدن ورقهاي کف و انولار بايد دقت شود تا آسيبي به فونداسيون تانك نرسد . سيمهاي پيانو را در امتداد زواياي ◦180-◦0 و ◦270-◦90 مي كشيم . اين سيمها به عنوان مبنا براي چيدن ورقهاي كف و تعيين موقعيت ورقهاي انولار روي فونداسيون بكار مي روند . ورق ريزي بايد از مرکز تانک به سوي محيط انجام شود .
2) به دليل کشيدگي جوشها ، مي توان روي هم افتادگي ورقهاي کف را بيشتر از ابعاد موجود در نقشه در نظر گرفت .
3) قطر بيروني ورقهاي انولار مي تواند 20 تا 30 ميلي متر بيش از ابعاد موجود در نقشه باشد . این مورد در خصوص مخازن با قطر بزگ توصیه می گردد . زیرا مطابق با استاندارد بایستی حداقل 50 میلیمتر ورق انولار از نشیمنگاه شل کورس اول بیرون تر باشد.
4) بعد از چيدن ورقهاي كف بايد محل اتصال آنها به فواصل 500 میلیمتر و به طول حداقل 25 میلیمتر خال جوش زده شود
5) ورقهاي انولار مطابق با نقشه هاي كارگاهي و نقاطي كه روي فونداسيون معين شده ، چيده مي شوند . در خصوص چیدمان ورقهای انولار بایستی دقت داشت که نقطه ابتدایی نسبت به صفر فوندانسیون رعایت گردد. دلیل این امر لزوم رعایت فاصله بین درز جوش ورقهای انولار با درز جوش ورقهای شل می باشد.
6) قبل از چيدمان ورقهاي انولار ، بايد ورقهاي پشت بند (back strip) را مطابق نقشه به آنها جوش داد . در خصوص خال جوش مربوط به ورقهای پشت بند تجربه شخصی من این است که بهتر است این خال جوش در قسمت داخلی جوش نباشد، بلکه در قسمت پشت ورق پشت بند زده شود. همچنین با استفاده از یک کاغذ معمولی درز انولار چک شود تا فاصله ای بین این دو نباشد. این مورد به این دلیل مهم است که پس از جوشکاری در صورت وجود فاصله مقداری گل جوش در این ناحیه باقی می ماند که باعث می شود که مفسر فیلم رادیوگرافی در بعضی موارد آن را به اشتباه ، ایراد مربوط به جوشکاری در نظر بگیرد.
جوشكاري صحيح ورقهاي انولار و كف
1)اصولا ، جوشكاري از مركز تانك شروع شده و به سوي محيط تانك ادامه مي يابد .
2)محل هائي كه به دليل تنش هاي حرارتي ناشي از جوشكاري دچار پيچش و تغيير شكل شده اند را مي توان با استفاده از روش برگشت (back step) اصلاح كرد .
3)پاس اول جوشكاري بايد به صورت منقطع و در اندازه هاي حدودا 300 میلیمتر انجام شود . در پاسهاي دوم به بعد ، جوشكاري به صورت پيوسته انجام مي شود .
4)300 ميليمتر ابتدائي محل اتصال ورقهاي انولار به يكديگر (محل قرارگيري ورقهاي شل روي ورقهاي انولار) بايد كاملا جوشكاري شده و پيش از جوشكاري ورقهاي شل به انولار مورد بازرسي به وسیله پرتونگاری قرار گيرد .
5) بعد از تكميل جوشكاري ورقهاي شل ، بايد ورقهاي انولار را به طور كامل به ورقهاي كف جوش داد .
6) چيدمان و جوشكاري ورقهاي كف هيچ گونه محدوديتي نداشته و ارتباطي به چيدمان ورقهاي انولار ندارد ، بنحويكه جوشكاري ورقهاي كف را مي توان قبل از چيدن ورقهاي انولار تكميل كرد .
7) در تانكهاي داراي سقف شناور ، بعد از تكميل جوشكاري كف و بعد از مونتاژ حداقل يك كورس از ورقهاي شل ، مي توان ساخت سقف را شروع كرد . قبل از تكميل سقف ، ورقهاي انولار بايد به ورقهاي كف جوش شده و آزمايش شوند .
8) ورقهاي اسكچ مطابق با ابعاد واقعي در كارگاه بريده مي شوند .
9) برشكاري ورقهاي كف جهت قرارگيري Drain Sump بايد مطابق نقشه و توسط گروه عمران انجام شده و سپس نصب و جوشكاري Drain Sump آغاز شود .
10) بعد از جوشكاري ورقهاي كف ، مي توان Drain Sumpرا نصب كرد .
11) محل اتصال ورقهاي انولار (جوشهاي لب به لب) بايد مطابق با دستورالعمل NDT توسط تست RT مورد بررسي قرار گيرد .
12) جوشكاري اتصالات ورقهاي انولار بايد به روشي انجام شود که سبب هيچگونه پيچشي در اين ورقها نشود , بنابراين ورق انولار بايد به طور كامل بر روي ورق پشت بند خوابيده و محل اتصال آنها جوشكاري شود . در ابتدا بايد پاسي از جوشکاري روي کليه ورقهاي انولار انجام شود . بعد از سنباده زني و تميز کاري , مي توان پاسهاي بيشتري جوش داد .
13) جوشكاري ورقهاي انولار به ورقهاي کف بعد از جوشكاري محل اتصال ورقهاي انولار و جوشکاري ورقهاي انولار به ورق شل شروع مي شود .
14) بعد از جوشکاري ورقهاي انولار به يكديگر , و جوشکاري درزهاي عمودي ورقهاي کورس اول , و بعد از مونتاژ سه کورس از ورقهاي شل و جوشکاري دو رديف از درزهاي افقي ورقهاي شل , مي توان ورقهاي انولار را به کورس اول ورقهاي شل جوش داد .
15) وقتي گوشه ورقها با شعله بريده مي شوند , بايد دقت کرد که ورق زيري صدمه نبيند . قبل از جوشكاري نهايي بايد كليه خال جوش ها را با سنگ تميز كرد .
وکيوم تست
جوشها پس از تکميل بايد به کمک جعبه خلاء و با استفاده از کف صابون تحت آزمايش خلاء قرار گيرند . فشار خلاء موجود در جعبه بايد حدود 400 mmHg باشد .
نصب ورقهاي شل
پيش از مونتاژ ورقهاي کورس اول ، بايد دايره اي مطابق با نقشه موقعيت ، روي ورقهاي انولار يا ديواره بتني علامتگذاري شود . بعد از علامتگذاري محل هر کدام از اتصالات ورقهاي شل را روي دايره مشخص نمائيد . جهت كنترل مدور بودن کورس هاي بعدي بايد دايره اي مرجع به فاصله 100 ميليمتر درون دايره اول علامتگذاري شود .
مونتاژ ورقهاي کورس اول ، دوم و سوم
1) ورقهاي كورس اول توسط جرثقيل در موضعشان قرار گرفته و پس از تراز کردن , به زمين متصل مي شوند . همزمان با مستقر کردن ورقها , بايد آنها را لب به لب هم قرار داده و موقتا توسط ورقهاي محکم به هم مونتاژ کرد .
2) مونتاژ موقت ورقهاي کورس اول به ورقهاي انولار بايد توسط تکه هاي ورق انجام شده و هيچ خال جوشي نبايد زده شود .
3) بعد از نصب کورس اول ، اگر لبه ورقهاي شل روي هم بيافتد , بايد فاصله کافي بين ورقها (گپ) ايجاد شود .
4) بعد از نصب و قبل از جوشکاري ، مدور بودن ، تراز بودن و شاقول بودن ورقهاي كورس اول بايد چك شود .
5) جوشكاري اتصالات عمودي كورس اول بايد پيش از نصب ورقهاي كورس دوم تكميل شود .
6) نقطه شروع جهت نصب كورسهاي دوم به بعد بايد ◦90 نسبت به نقطه قبلي جابجا شود .
7) نصب كورس هاي بعدي بايد بعد از تكميل جوشكاري كورس قبلي انجام شود .
جوشكاري صحيح ورقهاي شل
1) پاس اول كليه اتصالات عمودي بايد توسط روش برگشت (back step) و به صورت سر بالا انجام شود . جهت جوشكاري پاس هاي بعدي بايد ابتد پاس قبلي توسط فرچه تميز كاري شود .
2) بعد از تكميل پاس دوم اتصالات عمودي ، مي توان پاس اول را از سمت مخالف سنگ زد .
3) در كليه اتصالات جوشكاري عمودي و افقي بايد نفوذ كامل فلز جوش در فلز مادر صورت گيرد .
4) بعد از تكميل جوشكاري كورس دوم ، جهت سهولت دسترسي به درون تانك ، مي توان دريچه بازديد را روي كورس اول بريد (لبه هاي برشكاري شده سنگ زده شود) .
5) الكترودها بايد به مدت 2 ساعت و در دماي 250- 300◦C نگه داشته شوند . دماي گرم كنهاي دستي بايد 80-100◦C باشد .
استانداردهاي مونتاژ
1) ميزان عدم هم راستايي مجاز در ورقهاي شل به صورت زير مي باشد :
i) اتصالات عمودي
نبايد از 10% ضخامت ورق يا 6/1 ميليمتر بيشتر باشد .
ii) اتصالات افقي
نبايد از 20% ضخامت ورق بالائي بيشتر باشد در مورد ورقهاي ضخيم تر از 19 ميليمتر نيز نبايد از 2/3 ميليمتر بيشتر شود .
مونتاژ سقف شناوري
نصب پايه هاي موقت
1) مکان پايه هاي موقت (Temporary Roof Supports) بايد مطابق با نقشه روي عرشه پائيني علامتگذاري شود .
2) بعد از انجام بازرسي از موقعيت پايه هاي موقت ، جوشكاري آغازمي شود .
3) تنظيم موقعيت پايه ها با استفاده از ريسمان انجام مي شود .
چيدمان ورقهاي عرشه پائيني سقف
چيدن ورقها مطابق نقشه انجام مي شود . بايد توجه شود که حد مجاز روي هم افتادگي ورقها بايد کاملا مطابق با اندازه هاي نشان داده شده در نقشه باشد .
جوشکاري عرشه پائيني سقف
بايد توجه داشت جهت جلوگيري از باد کردگي ورقها تعدادي از تقاطع ها (+) نبايد جوشکاري شوند , تنها بعد از اطمينان از اينکه هيچکدام از ورقها باد نکرده اند مي توان آنها را جوشکاري کرد .
سوار کردن حلقه ها (Rim Plates) ، ديواره ها(bulk heads) و تراسها (truss)
1) به هنگام علامتگذاري موقعيت حلقه ها و ديواره هاي شعاعي روي ورقهاي عرشه پائيني , بايد موقعيت Rolling Ladder , Roof Drains و Gauge Pole نيز مشخص شود .
2) بعد از جوشکاري حلقه هاي ابتدائي , تراسها را سوار مي کنيم .
3) نصب حلقه هاي مياني مطابق با نقشه انجام مي شود .
4) ديواره هاي شعاعي را به صورت عمودي نصب مي کنيم .
5) بعد از جوشکاري ديواره هاي شعاعي , آنها را به حلقه ها جوش مي دهيم .
6) کليه جوشها بايد توسط گازوئيل تحت تست نشتي قرار گيرند .
7) چيدن ورقهاي عرشه بالائي سقف همانند عرشه پائيني است .
نصب پايه هاي دائمي (Pipe Supports)
1) علامتگذاري موقعيت پايه ها روي ميز کار مطابق نقشه انجام مي شود .
2) غلاف پايه ها بايد مطابق با نقشه به ورقهاي عرشه جوش داده شوند .
3) تنظيم يا تصحيح ارتفاع پايه ها و مونتاژ کردن آنها .
برداشتن پايه هاي موقت
وقتي پايه هاي دائمي به طور كامل نصب شدند ، بايد پايه هاي موقت را برداشت .
نصب متعلقات مربوط به شل مخزن
Shell Manhole , Water Sump , Nozzle
نصب متعلقات مربوط به سقف شناور
Deck manhole , Pontoon Manhole , Roof Drain , Emergency Drain لازم است كه مكان قرارگيري متعلقاتي كه در بالا ذكر شد مطابق نقشه علامتگذاري شود .
كورسهاي چهارم به بالا
ورقهاي شل از کورس چهارم به بعد مرحله به مرحله مونتاژ و جوشکاري مي شوند .
1- بعد از مونتاژ ورقهاي شل ، خال جوش زني بر روي تاپ انگل انجام شده و ورقهاي سخت كننده R مانند با خال جوش به تاپ انگل متصل مي شوند .
2- وقتي كه جوشكاري اتصالات عمودي كورسهاي چهارم به بالا تكميل شد ، اتصالات عمودي تاپ انگل نيز بايد جوشكاري شوند .
بادبند
3- چون بادبندها از قبل به صورت مدور ساخته مي شود لبه هاي آنها جز در موارد ضروري نبايد بريده شود .
4- جوشكاري بادبندها به شل بايد قبل از جوشكاري اتصالات افقي تكميل شود . جوشكاري جوشهاي افقي بايد به صورت منقطع و به فواصل 1 متر انجام شود ولي در پاسهاي بعدي مي توان به صورت پيوسته جوشكاري كرد .
سيستم زه کشي سقف (Roof Drain System)
بعد از نصب پستهاي مربوط به سقف ، سيستم فاضلاب سقف و نگهدارنده ها مطابق با نقشه جوشكاري شده و بعد از تكميل جوشكاري توسط تست روغن نافذ آزمايش شوند .
سيستم آب بندي (Sealing System)
قبل از نصب سيستم آب بندي , کليه موانع را بايد از بالاي پونتونها برداشت . سيستمهاي آب بندي و پوشش ها بايد مطابق نقشه و دستورالعملهاي نصب مونتاژ شوند .
بازرسي و تستها
بازرسي و تست هاي مربوطه توسط ناظر کارفرما انجام مي شود . گزارش بازرسي و آزمايش ها بايد جهت بازنگري و تصويب به کارفرما ارائه شوند .
تست پر کردن مخزن با آب
موارد زير بايد قبل از انجام آزمايش چک شوند :
1) کليه جوشکاريها بايد تکميل شده باشند .
2) کليه تستهاي راديوگرافي بايد انجام شده باشند .
3) لوله کشي موقت جهت انجام تست بايد تکميل شده باشد .
4) تميزکاري درون تانک و برداشتن جيگهاي موقت انجام شده باشد .
5) کليه دريچه هاي موجود بر روي شل بايد توسط شيرها يا درپوشهاي مناسب مسدود شوند .
6) منهولهاي سقف بايد باز باشند .
7) همسطح بودن (تراز بودن) فونداسيون بايد در نقاطي مشخص اندازه گيري شود .
8) جهت جلوگيري از نشست آني مخزن ، ميزان افزايش ارتفاع آب در مخزن بايد کمتر از 5 متر در روز باشد .
انجام بازرسي هنگام پر شدن مخزن
1) در صورت نشست فونداسيون پيمانکار بايد موضوع را فورا به ناظر گزارش دهد .
2) کنترل اينکه آيا آب از محل جوشکاريها نشت مي کند يا نه .
رنگ کاري
1) آماده سازي سطح و رنگ کاري بايد مطابق مشخصات مصوب کارفرما انجام شود .
2) پيش از استفاده از آستر (جهت ممانعت از زنگ زدن تانک)، تانک بايد کاملا تميز بوده و عاري از آب و مواد باقيمانده خارجي و ته الکترودها باشد .
آماده سازی مدارک فنی
فاز آماده سازی مدارک فنی جزء مهمترین و حساس ترین قسمتهای مربوط به بازرسی می باشد. اهمیت این قسمت وقتی مشخص می گردد که با نگاه به سیر روند اجرای پروژه ، این مطلب را به خاطر بسپاریم که پایه گذاری موارد مربوط به فرمتها ، روال ، ایستگاههای بازرسی و بسیاری مطالب دیگر باعث موفقیت یا عدم موفقیت گروه بازرسی در کنترل کیفی فرایند ساخت خواهد بود.
به طور کلی مدارک و مستندات فنی مورد نیاز در بازرسی مخازن ذخیره را می توان به صورت زیر بیان کرد :
1-ITP
2-Fabrication & Erection Procedure
3-WPS(Welding Procedure Specification
4-PQR(Procedure Qualification Record
5-NDT Procedure (Nondestructive Testing Procedure
6-Painting Procedure
7-PWHT Procedure ( Post weld Heat Treatment Procedure
8-Hydro static test Procedure
9-Welding Map
آزمایشات غیر مخرب NDT درمراحل بازرسی مخازن ذخیره
آزمایشات غیر مخرب جهت بررسی کیفیت مواد و قطعات دارای کاربرد می باشند. در بسیاری موارد از این آزمایشات جهت بررسی کیفیت جوشکاری انجام شده بر روی سازه های مختلف استفاده می شود ، ولی باید به یاد داشت کاربرد آزمایشات غیر مخرب بسیار فراتر از کنترل کیفیت جوشکاری بوده و در تجزیه و تحلیل میزان عمر سازه ها و خواص الکتریکی ، مکانیکی و ... دارای کاربردهای فراوان می باشد.
آزمایشات غیر مخرب به روشهایی اطلاغ می گردد که با بررسی سازه و بدون ایجاد تخریب و تغییر در آن نسبت به شناسایی و مشخص نمودن خواص مورد نظر اقدام نمایید. روشهای گوناگونی بعنوان آزمایشات غیر مخرب شناخته می شوند. مراجع گونگونی برای انجام آزمایشات غیر مخرب معرفی شده اند. هر یک از استانداردهای ISO,BS,EN,DIN,… روشهای مختلفی را برای انجام آزمونهای غیر مخرب معرفی نموده اند. بعنوان یکی از مراجع که در آزمونهای غیر مخرب استفاده فراوانی دارد می توان به استاندارد ASME Sec V اشاره کرد. از دلایل محبوبیت و کاربرد این استاندارد مجتمع بودن آن است. این استاندارد برخلاف استانداردهای اروپایی در یک کتاب مرجع ارائه شده است. لیستی از روشهای ارائه شده در این استاندارد را می توان بشرح زیر بیان نمود.
- Article 1 General Requirements
- Article 2 Radiographic Examination
- Article 4 Ultrasonic Examination Methods for In-service Inspection
- Article 5 Ultrasonic Examination Methods for Materials and Fabrication
- Article 6 Liquid Penetrant Examination
- Article 7 Magnetic Particle Examination
- Article 8 Eddy Current Examination of Tubular Products
- Article 9 Visual Examination
- Article 10 Leak Testing
- Article 11 Acoustic Emission Examination of Fiber-Reinforced Plastic Vessels
- Article 12 Acoustic Emission Examination of Metallic Vessels During PressureTesting
- Article 13 Continuous Acoustic Emission Monitoring
برای انجام آزمایشات غیر مخرب میبایست دستورالعملهایی از قبل توسط افراد ذی صلاح تهیه شود که به عنوان مبنا و مرجع توسط بازرسین مورد استفاده قرار داده شود . دلیل این امر این است که در حقیقت با تدوین روش مناسب و درست و درج معیارهای پذیرش متناسب با حساسیت سازه از صرف زمان وهزینه بیهوده جلوگیری می شود. در هر دستورالعمل مربوط به آزمایشهای غیر مخرب جزئیات زیر باید بدقت ذکر شود :
۱-Scope
بسیار مهم است که در یک رویه کاری مشخص شود که این روش برای استفاده در چه شرایطی بوده و در صورت تغییر کدامین شرایط نمی توان از این روش کاری استفاده کرد. مطالبی که در این قسمت بصورت معمول ذکر می شوند:
- موادی که با این روش تست قابل آزمایش می باشند.
- شرایط خاصی که نگارنده روش آزمایش با در نظر گرفتن آنها نسبت به آماده سازی این مدرک اقدام نموده است.
۲-Reference Standards
هماننگونه که مشخص است در این قسمت استانداردهای مرجع که در نگارش این مدرک استفاده شده اند ذکر می شود.
۳-Personal Qualification
در این قسمت مهارت مورد نیاز برای انجام آزمایشات مطابق این رویه ذکر می گردد. ذکر یک مطلب در این قسمت ضروری به نظر می رسد. بسیاری از دوستان در دستورالعمل های خود بعنوان مثال ذکر می کنند SNT- TC-1A Level I or II . اما در بسیاری از موارد دارا بودن تنها مدرک کافی نیست و بنظر بهتر است که سابقه کاری مفیدی جهت کار در زمینه مورد نظر ذکر شود.
۴-Equipment
در این قسمت مشخصات دستگاهها و یا مواد مورد استفاده را که مورد قبول می باشند ذکر می کنند. در بسیاری از موارد بایستی که جهت تکمیل این قسمت به لیست شرکتهای مورد تایید کارفرما رجوع کرد.
۵-Technical Detail
در این بخش اطلاعات مربوط به روش انجام آزمایش قرار می گیرد.
۶-Acceptance Criteria
حدود مورد پذیرش عیوب بایستی مطابق با استاندارد مورد نظر استخراج شده و در این قسمت جای داده شود.
۷-Blank Format
در پایان نمونه گزارشی برای ثبت اطلاعات هر آزمایش در قسمت انتهایی قرار می گیرد.
بازرسی چشمی(VT)
تعریف:
در این نوع بازرسی، شخص با استفاده از تجربیات و آموزشهای گذرانده نسبت به بررسی سازه مورد نظر اقدام نموده و مشکلات قابل مشاهده را ذکر می نماید. در این روش ممکن است که بازرس نسبت به بازرسی با چشم غیر مسلح اقدام نماید یا اینکه با استفاده از وسایلی چون ذره بین ، بوروسکوب ، گیج و... اقدام به بررسی نماید.
اصول :
پارامترهای مهم در بازرسی چشمی عبارتند از شدت نور محیط و نوع نور محیط ، شرایط سطح وآماده سازی سطح مانند تمیز كاری قطعه و زاویه نور تابشی می باشد. زاویه نور تابشی بدین دلیل دارای اهمیت است که بعضی از عیوب سطحی فقط تحت تابش نور صحیح ( تابش نور تحت زاویه مناسب )آشكار می شوند .
کاربرد :
تمام عیوب ظاهری اعم از عیوب سطحی ، تركهای سطحی ،نادرستی شكل ، انحرافات در اندازه و غیره را می توان با بازرسی چشمی مشخص نمود. بازرسی چشمی به عنوان یك روش بازرسی غیر مخرب برای مواد خام و محصولات نیمه تمام یا تمام شده مورد استفاده می باشد .با بازرسی چشمی پیش از عملیات تولید، در مرحله آماده سازی ، حین تولید و همینطور بررسی نهائی می توان از خصوصیات سطحی و علائم مشخصه دیگر در مورد محصول داوری نمود . بازرسی چشمی صحیح قطعات و بررسی شكل ظاهری آنها چه با چشم غیر مسطح ، چه با ذره بین یا بروسکوب انجام شود ، در تشخیص عیوب متالورژیكی حائز اهمیت است و می تواند مبنای برنامه ریزی برای بازرسی های بعدی باشد . بعلاوه بازرسی چشمی اطلاعات مفیدی بدست می دهد كه گاهی اوقات این اطلاعات برای حل مسئله كفایت می كند.
مزایا :
بازرسی چشمی ساده و ارازن است و به وسایل و دستگاه های گرانقیمت احتیاج ندارد از شرایط سطحی قطعه و ارزیابی دقیق ظاهر آن خیلی چیزها روشن می شود.
محدودیت :
با چشم غیر مسلح تنها نقص های نسبتاٌ بزرگ كه باعث شكستگی پوسته شده اند ، آشكار می شود كارایی بازرسی چشمی را با استفاده از ذره بین با قدرت كم و میكروسكوپ می توان افزایش داد .
استانداردهای مرجع :
علاوه بر استاندارد ASME می توان عیوب مرتبط با جوش را در یک دسته بندی مناسب در استاندارد ISO 5817 یافت. این استاندارد به معرفی کلیه عیوب جوشکاری پرداخته است . فارق از اینکه این عیوب قابل روئیت با چشم مسلح یا غیر مسلح می باشند یا خیر.
آزمایش مایعات نافذ(PT)
تعریف :
آزمایش مواد با مایع نافذ از قدیمی ترین ، اقتصادی ترین و ساده ترین روشهای كشف شده برای شناسایی عیوب سطحی غیر قابل تشخیص با چشم غیر مسطح می باشد. اساس این روش مبتنی بر قابلیت نفوذ بعضی از مایعات با استفاده از خاصیت موئینگی به داخل حفره ها و تركهای خیلی نازك است . بنا بر این برای آشكار سازی نقص هایی كه سبب شكستن سطح كار شده اند ،به كار می رود، این مایعات كشش سطحی كم و قابلیت تر كنندگی خوب نسبت به ماده آزمایش شونده دارند و قادرند روی سطح این مواد قشر نازكی تشكیل دهند .
اصول :
بطور عمومی همه ما روش بازرسی با مواد نفوذ كننده را دارای شش مرحله اساسی می دانیم :
- آماده سازی سطح
- كاربرد مواد نفوذ كننده و اعمال زمان برای نفوذ
- برداشت مواد نافذ اضافی
- كاربرد مواد ظهور و اعمال زمان برای ظهور
- مشاهده و بازرسی
- تمیز کاری نهایی
انواع روشها :
در عمل مواد نفوذ كننده را به وسیله یكی از روشهای متداول بر روی سطح قطعه اعمال میکنند. روش برگزیده به اندازه ،شكل وتعداد قطعات مورد بازرسی بستگی دارد. بازرسی قطعه در محل نیز یكی از عوامل گزینش میباشد. مایعات نافذ ، چه مرئی ، چه فلورئوسنت می توانند بوسیله هر یك از راه های ذیل اعمال شوند :
غوطه وری: كل نمونه به داخل یك مخزن مایع نافذ ، فرو برده می شود .
پاشش: معمولاً با استفاده از پمپ مدار بسته كم فشار یا از قوطی های پاششی فشار ، مایع نافذ روی سطح پاشیده می شود.
ریختن: مایع نافذ با یك وسیله به سادگی روی سطح ریخته می شود
معمولا برای بازرسی چندین قطعه نسبتا كوچك بهتر است از روش فرو بردن كامل به درون مخزن حاوی مایع نفوذكننده استفاده شود. قطعات را باید پیش از غوطه وری كاملاخشك كرد زیرا آب یا حلالهای تمیز كننده به جا مانده با آلوده شدن به ماده نفوذ كننده از نفوذ آن جلوگیری میكنند. در حین غوطه وری قطعه ، باید دقت شود كه حبابهای هوا ایجاد نشوندوتمام سطوح بازرسی كاملا خیس شوند . معمولا قطعات را به مدت معینی در مایع فرو می برند و سپس بیرون می آورند . در خلال این مرحله ، باید دقت شود كه مایع نفوذ كننده از تمام منافذ خارج شده باشد . قطعاتی را كه آثار ماده نفوذ كننده بر روی سطحشان وجود دارد ، پس از خشك كردن باید دوباره غوطه ور ساخت .
معمولاً از شیوه سیلابی برای بررسی سطوح بزرگ قطعات ساده استفاده می شود . معمولاً ماده نفوذ كننده را با فشار پایینی كه موجب ذره ای شدن سیال نمی شود ، بر روی سطح می پاشند . باید مطمئن شد كه ماده نفوذ كننده تمام سطح مورد بررسی را پوشانده ، و سطح در تمام مدت نفوذ مرطوب باشد .
هنگامی كه تنها بررسی قطعات تكی یا بازرسی قطعات در محل لازم است ، ماده نفوذ كننده را به وسیله قلم مو یا از طریق قوطی اسپری به كار می برند . برای قطعات پیچیده تر بهتر است از قلم مو استفاده شود . هنگام استفاده از شیوه سیلابی از خشك شدن ماده نفوذ كننده بر روی سطح باید جلوگیری كرد .
کاربرد :
امروزه ، بازرسی با مواد نفوذ كننده رنگی ، روش صنعتی مهمی است و برای تعیین نقص هایی مانند ترك ، جدا لایگی ، رویهم افتادگی و منطقه های تخلخل سطحی در بسیاری قطعات به كار می رود . این روش تقریباٌ برای همه قطعات قابل استفاده است ، اعم از اینكه قطعه بزرگ باشد یا كوچك ، شكل ساده داشته باشد یا پیچیده ؛ این روش برای بازرسی فرآورده های ریختگی و كار شده فلزات آهنی و غیر آهنی و همچنین آلیاژ ها ، سرامیك ها ،شیشه آلات و برخی قطعات پلیمری به كار می رود.
مزایای بازرسی با مایع نافذ :
علائم وجود عیب روی خود قطعه ظاهر می شود
محدودیتی برای اندازه و شكل جسم مورد كنترل وجود ندارد
این روش برای بازرسی قطعات كوچك نیز مناسب است
مایعات نافذ دارای قابلیت نفوذ فوق العاده ای در داخل تركها بسیار نازك بوده و با تنوع در تركیب و تحت شرایط متنوعی می توانند برای بازرسی مواد مختلفی بكار روند .
متدهای بازرسی دیگر مانند ذرات مغناطیس اغلب به دو بازرسی جداگانه یا بیشتر نیاز دارد ولی در مورد مایع نافذ یكدفعه كنترل كافی است .
فرآیند بازرسی با مایع نفوذ كننده نسبتاً ساده است ، زیرا شامل هیچ نوع سیستم الكترونیكی نیست ، و تجهیزات مورد نیاز ارزانتر از دیگر تجهیزات سیستم های آزمون های غیر مخرب است . معمولاًاجرای روشها و استاندارد های بازرسی برای قطعات تولیدی خاص ساده تر از روشهای پیچیده تر دیگر است . این روش برای بازرسی همه نوع مواد بجز مواد متخلخل به كار می رود ، و درپاره ای موارد ، حساسیت آن بیش از بازرسی به وسیله ذرات مغناطیسی است . بازرسی با مواد نفوذ كننده در واقع برای همه قطعات با هر اندازه و شكلی مناسب است و برای كنترل كیفی تولیدات نیمه تمام و تمام شده و همچنین بازرسی مستمر قطعات در حین كار به كار می رود .
محدودیت بازرسی با مایع نافذ :
فقط عیوب منتهی به سطح را میتواند كشف نماید .
اگر سطح جسم متخلخل باشد مایع اضافی را نمی توان به آسانی از سطح قطعه پاك نمود و در نتیجه علائم عیب با علائم نفوذ موجود در این تخلخلها مخلوط شده و بخوبی قابل تشخیص نمی باشد .
با وجودی كه مایع نافذ در حدود درجه حرارتهای نسبتاً وسیعی موثر است معهذا درجه حرارتهای خیلی كم و خیلی زیاد برای كار مناسب با مایع نافذ سازگار نمی باشد .
حفاظت مایع نافذ از آلوده شدن به مواد خارجی مخصوصاً آب مسئله ایست و در آماده كردن قطعات برای بازرسی و حفاظت ظروف حاوی مایع نافذ از رطوبت گرد و خاك یا سایر مواد خارجی باید كوشید.
آشكار سازی نقصهای زیر سطحی به روش های بازرسی دیگر نیاز ذارد . نا همواری های سطحی و تخلخل مواد از عوامل دیگر عدم كارایی این سیستم اند . این مورد ، به ویژه می تواند نشانه های غلط به وجود آورد ، زیرا هر گونه خلل و فرج را به عنوان نقص بالقوه ای ثبت خواهد نمود.
آزمایش به روش ذرات مغناطیسی(MT)
تعریف :
بازرسی به روش مغناطیس كردن ذرات روشی حساس برای تعیین محل نقصهای سطحی و برخی نقصهای زیر سطحی در مواد فرو مغناطیس است
اصول :
پارامترهای اصلی این روش مبتنی بر مفهوم های نسبتاً ساده ای است .در اصل ، اگر قطعه مورد آزمایش از جنس مغناطیس شونده باشد و از آن مغناطیس عبور داده شود . خطوط قوای مغناطیس در برخورد با ناپیوستگی ها (تقریباً) عمود بر جهت میدان تغییر مسیر می دهند و میدان نشت قویی را به وجود می آورند . این میدان نشت در سطح و بالای قطعه مغناطیده قرار دارد ، حال چنانچه ذرات ریز مواد مغناطیس شونده بصورت خشك یا معلق در مایع یر روی سطح قطعه پاشیده شود ، در محل وجود عیب ، تجمع نموده پل مغناطیسی كه به این ترتیب تشكیل می شود ، محل ، اندازه و شكل ناپیوستگی را تعیین می كند.
برای آزمایش ذرات مغناطیسی ، سطح قطعه بایستی نسبتاً صاف باشد .چه در غیر اینصورت در اثر نا صافی و شیارهای سطحی ، ذرات پل میزنند و احتمالاً ترك در زیر پوشش آنها مخفی می ماند . گاهی از رنگ سفید زود خشك شونده زمینه سفیدی بوجود آورده میشود تا براده سیاه در متن سفید به خوبی مشاهده گردد . گاهی هم براده ها را رنگ می زنند تا راحت تر دیده شوند .اگر براده با رنگ فلوئورسنت آغشته گردند در زیر تابش نور ماوراء نفش به وضوح دیده می شوند .خاصیت مغناطیس را در قطعه به وسیله آهنرباهای دائم ، آهنرباهای الكتریكی ، یا با گذراندن جریانهای قوی از درون یا پیرامون آن می توان القاء كرد . این شیوه به سبب امكان تولید میدانهای مغناطیسی شدید در درون قطعات ، در عملیات كنترل كیفیت كاربرد گسترده ای دارد . این روش در تشخیص و آشكار سازی تركها حساسیت خوبی دارد.چرخ دنده ها محورها و قطعات مشابه را پس از زمایش مغناطیس زدائی می كنند تا ضمن كار و از ایجاد جریانهای گردابی جلوگیری کرده و تراش براده ها و ذرات را جذب ننمایند .
انواع روشها :
تشخیص عیوب در قطعه توسط بازرسی ذرات مغناطیسی به روشهای پیوسته و پسماند، میدانهای مغناطیسی، میدان حلقوی، میدان مغناطیسی طولی، میدان مغناطیسی چرخنده انجام میشود.
كاربردها :
كاربردهای صنعتی اصلی بازرسی به وسیله ذرات مغناطیسی عبارتند از : بازرسی فرآیندی ، بازرسی نهایی . بازرسی دریافتی ، تعمیرات جزیی و كلی . قطعات خریداری شده نیمه تمام و هم مواد اولیه برای تشخیص نقصهای اولیه آزمون می شوند. بازرسی میلگردها ،تسمه ها ، شمشهای آهنگری و ریختگی های ماسه ای وارده با این روش انجام می شود . در صنایع حمل و نقل (جاده ای ، راه آهن ، هوایی و دریایی) بر اساس برنامه های منظم تعمیرات كلی موجود ،قطعات حساس را برای شناسایی تركها بازرسی می كنند . میل لنگها ، قابها ، چرخ لنگرها ، قلابهای جرثقیل ، محورها ، پره های توربین بخار و اتصال دهنده ها نمونه ای از قطعات آسیب پذیر به شكست ، به ویژه شكست ناشی از خستگ اند ؛ و بنا براین به بازرسی منظم نیاز دارند .، سیستم بازرسی به وسیله ذرات مغناطیسی را می توان به سادگی خودكار كرد و در نتیجه ، بازرسی مطمئن و نسبتاً بدون زحمتی انجام داد . در حالی كه سیستم خودكار در حال انجام وظایف مكانیكی خود است ، مسئول بازرسی می تواند تمام وقت خود را صرفاً به بازرسی اختصاص دهد . آهنگ تولید متناسب با عملیات متعددی است كه همزمان در ایستگاه های مختلف انجام می شود . هزینه خودكار سازی در مقایسه با هزینه نیروی انسانی برای چندین واحد منفرد دستی كه برای دستیابی به همان آهنگ های تولیدی لازم است ، توجیه پذیر خواهد بود
مزایای آزمایش با ذرات مغناطسی :
- الف – یکی از قابل اعتمادترین متدها برای پیدا كردن تركها سطحی ، خصوصاً تركهای خیلی ظریف و كم عمق می باشد .
- ب – علائم وجود و یا عدم وجود عیب روی خود قطعه ظاهر می شود
- ج – كنترل سریع بوده و انجام آن آسان می باشد . اپراتور می تواند طرز كار را بدون آموزش طولانی یا خیلی فنی به آسانی بیاموزد .
- د- محدودیتی برای اندازه یا شكل قطعه مورد آزمایش وجود ندارد .
- ه – تركها اگر با ماده خارجی دیگری پر شده باشند نیز در این روش پیدا می شوند .
- و – در حالت عادی پاك كردن قبلی نمونه لازم نیست .
- ز – پوشش نازك رنگ یا سایر پوشش های غیر مغناطیسی مانع كار نخواهد شد .
- ر – در این متد از تجهیزات الكترومكانیكی استفاده می شود كه پرداخت و ظرافت چندانی لازم نداشته و می تواند در كارگاه ساخته شود . نگهداری آن نیز آسان است .
- - این متد می تواند بطور خود كار بكار رود و نسبتاً ارزان است .
محدودیت آزمایش با ذره مغناطیس
- الف – این روش فقط برای مواد فرو مغناطیس قابل استفاده است .
- ب – در مورد عیوب غیر سطحی دقیق نمی باشد .
- ج - میدان مغناطیسی بایستی در جهتی ایجاد شود كه سطح اصلی عیب را قطع نماید و این مسئله ایست كه اپراتور با آن مواجه می شود و بهمین دلیل گاهی به دو مرتبه بازرسی كردن و یا بیشتر نیاز دارد .
- د - مغناطیسی زدائی پس از انجام آزمایش اغلب ضرورت پیا می كند
- ه – بعد از انجام ازمایش و مغناطیس زدائی ، تمیز كردن قطعه و جدا كردن ذرات مغناطیس چسبیده به سطح ممكن است ضروری باشد .
- و – هنگام آزمایش قطعات دارای شكل پیچیده تولید میدان مغناطیس در جهت مناسب اغلب مسئله است .
- ز- هنگام آزمایش قطعات ریخته گری شده خیلی بزرگ ، جریان بر ق خیلی زیادی مورد لزوم است .
- ر – برای اجتناب از گرم شدن ناحیه و سوختن قطعات با سطوح صیقلی یا در محلهای تماس برق با این سطوح مراقبت زیادی لازم است .
- ط – برای مغناطیس كردن ، جابجا كردن قطعات ضروری است و این عمل مخصوصاً وقتی كه تعداد زیادی از قطعات كوچك مورد كنترل واقع می شوند وقت گیر می باشد .
- ی – با وجود اینكه علائم وجود عیب به آسانی دیده می شود ، معهذا گاهی در تفسیر علائم تجربه و مهارت لازم است . البته در مقایسه با متدهای دیگر مثل رادیو گرافی و التراسونیك آزمایش با ذره مغناطیسی خیلی ساده تر می باشد .
بازرسی با امواج مافوق صوت(UT)
تعریف :
روش های فراصوتی كاربرد بسیار گسترده ای در تعیین نقص های درونی مواد دارند ، با وجود این از آنها می توان برای تعیین ترك های زیر سطحی نیز استفاده كرد. آزمون های فراصوتی ،افزون بر بازرسی قطعات تكمیل شده ،برای بازرسی كنترل كیفیت مراحل مختلف تولید قطعاتی همچون لوحه ای نورد شده نیز به كار می روند. معمولاٌ از این روش ها برای بازرسی قطعات و مجموعه های در حین كار نیز استفاده می شود .
اصول :
در این روش صوت از میان محیط های جامد به راه های مختلف منتشر می شود، و تغییرات را برروی صفحه دستگاه التراسونیك نمایان می سازد و به این طریق اپراتور عیوب داخلی قطعه مورد آزمایش را تشخیص می دهد.
انواع روشها :
وجود نقص را در ماده با استفاده از امواج فراصوتی به وسیله روش عبوری یا بازتاب می توان آشكار ساخت .
کاربرد : روش های فراصوتی كاربرد بسیار گسترده ای در تعیین نقص های درونی مواد دارند ، با وجود این از آنها می توان برای تعیین ترك های زیر سطحی نیز استفاده كرد. آزمون های فراصوتی ،افزون بر بازرسی قطعات تكمیل شده ،برای بازرسی كنترل كیفیت مراحل مختلف تولید قطعاتی همچون لوحه ای نورد شده نیز به كار می روند . معمولاٌ از این روش ها برای بازرسی قطعات و مجموعه های در حین كار نیز استفاده می شود .
آزمایش پرتونگاری صنعتی(RT)
تعریف :
بازرسی رادیوگرافی روشی از آزمایشات غیر مخرب می باشد كه توسط تشعشات رادیواكتیو یا پرتو ایكس ساختار داخلی قطعات مورد آزمایش را نمایان می سازد. در این روش انرژی از یك سمت وارد قطعه می شود و از سمت دیگر از آن خارج می شود و این انرژی روی وسیله ای (به عنوان مثل فیلم) ثبت می شود.
اصول :
اساس بازرسی رادیوگرافی بر مبنای دو اصل می باشد نفوذ و جذب، در این روش باید برای هر قطعه ای انرژی انتخاب شود كه علاوه بر اینكه قابلیت نفوذ و عبور از قطعه را داراست مقداری از آن انرژی به ذرات داخل قطعه برخورد كرده و جذب آن قطعه شود.
کاربرد :
اكثر قطعات فلزی و غیر فلزی، مواد غذایی
مزیت های این روش :
- برروی اكثر قطعات می توان آزمایش رادیوگرافی انجام داد.
- تصویر دائمی به ما می دهد.
- عیوب داخلی و عیوب مجموعه ها را آشكار می سازد.
- مقدار حساسیت با تغییر انرژی قابل تنظیم است.
محدودیت های این روش :
- دسترسی به دو طرف قطعه مورد نیاز است.
- قطعات ضخیم به دلیل محدود بودن انرژی منابع موجود قابل رادیوگرافی نمی باشد.
- رادیوگرافی برروی قطعات پیچیده مشكل می باشد.
- عیوب موازی با سطح در این روش قابل تشخیص نمی باشند.