آموزش عملی جوشکاری
هدف از آموزش های عملی جوشکاری
جوشکاری امروزه جزء صنایع مادر محسوب می شود، زیرا که درنصب و راه اندازی اغلب کارخانجات و تاسیسات صنعتی و ساخت اغلب ساز ها و تجهیزات صنعتی از جوشکاری استفاده می گردد و کسانی که در این امر یعنی جوشکاری فعالیت فنی خود را آغاز نمایند، از امنیت شغلی بالایی در آینده برخوردار خواهند شد و به سادگی می توانند وارد بازار کار گردیده و مهارت فنی و عملی و نیز تجربه لازم را نیز به دست آورند. امروزه در سراسر دنیا سازههای فولادی و غیره بطور چشمگیری گسترش پیدا کرده است اهمیت جوش در سازهای فولادی بر کسی پوشیده نیست. وقتی ما میتوانیم مخازن تحت فشار ، خطوط لوله انتقال گاز را به آسانی جوش دهیم، وقتی ما میتوانیم گاز ترش با فشار بالا را از دل خلیج فارس با خط لوله جوش داده شده زیردریائی به عسلویه انتقال دهیم و آنرا پالایش کنیم، وقتی کشتیها و دیگهای بخار، مبدلهای حرارتی و .. را جوش میدهیم، بدین معناست که مهارت جوشکاری یکی از مهارت های کلیدی در جهان امروز می باشد. همچنین بدلیل کمبود افراد متخصص در این رشته، بازار کار این حرفه نه تنها در سراسر کشور، بلکه در بسیاری از کشور های صنعتی دنیا از جمله کانادا و استرالیا بسیار پر طرفدار و گواهینامه های آموزشی صادر شده توسط این موسسه، مناسب برای ارائه به داخل و خارج از کشور می باشد. هدف از این آموزش ها، تربیت نیروی انسانی ماهر است که قادر باشند براساس دانش و مهارتهای فنی و تخصصی صنعت جوش در زمینههای ساخت و تولید، نصب و مونتاژ، تعمیر و بازسازی صنایع کشور فعالیت نمایند و براساس علوم و فنون فراگرفته شده به ایجاد اتصالات جوشی قابل اطمینان قطعات مختلف صنعتی بپردازند. موسسه آریا آزمون صنعت با دارا بودن بیش از 15 سال سابقه در خصوص ارایه آموزش های جوشکاری ، بازرسی جوش و NDT در این خصوص در کشور پیشتاز بوده و آماده ارایه خدمات مذکور در محل کارفرما و یا در کارگاه آموزشی این موسسه می باشد.
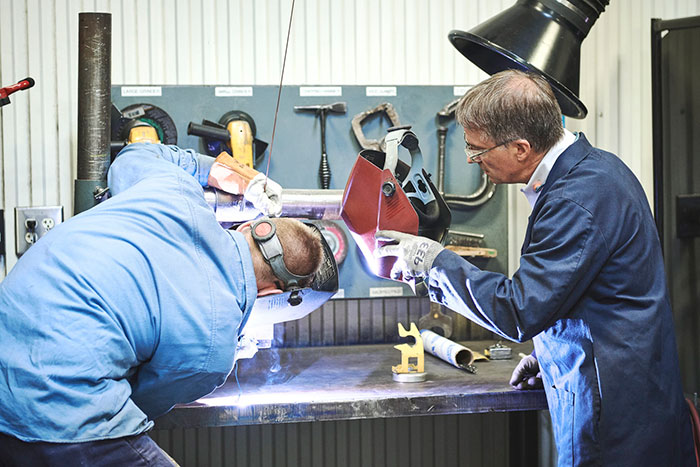
مدت زمان پیشنهادی دوره آموزش عملی جوشکاری
مدت زمان مورد نیاز برای آموزش بسته به فرایند جوشکاری، سطح فعلی هنرجو و سطح مورد انتظار تعین میگردد، لاکن حداقل مدت زمان پیشنهادی برای فرایند های مختلف به شرح ذیل ارایه میگردد.
کد دوره | عنوان دوره آموزشی | مدت دوره (ساعت) | مدت دوره (روز) | مدت ساعات تئوری | مدت ساعات کارگاه | نوع گواهینامه |
---|---|---|---|---|---|---|
1 |
دوره جامع آموزش جوشکار تایید صلاحیت شده سطح I
AWS QC-10
Certified Entry Welder
|
120 | 15 | 32 | 88 | گواهینامه جوشکار تایید صلاحیت شده طبق استاندارد AWS QC 10 + گواهینامه صلاحیت جوشکار در روشهای SMAW,GMAW,GTAW,FCAW طبق استاندارد های ASME,AWSو یاEN |
2 | آموزش جوشکاری در روش SMAW روی ورق های فولادی | 48 | 6 | 8 | 40 | گواهینامه تایید صلاحیت جوشکار ورق طبق استاندارد های ASME,AWS و یاEN |
3 | آموزش جوشکاری در روش SMAW روی لوله های فولادی | 48 | 6 | 5 | 43 | گواهینامه تایید صلاحیت جوشکار لوله طبق استاندارد های ASME,AWSو یاEN |
4 | آموزش جوشکاری در روش(TIG) GTAW روی ورق های فولادی | 48 | 6 | 8 | 40 | گواهینامه تایید صلاحیت جوشکار ورق طبق استاندارد های ASME,AWSو یاEN |
5 | آموزش جوشکاری در روش(TIG) GTAW روی لوله های فولادی | 48 | 6 | 5 | 43 | گواهینامه تایید صلاحیت جوشکار لوله طبق استاندارد های ASME,AWSو یاEN |
6 | آموزش جوشکاری در روش(TIG) GTAW روی فولادهای زنگ نزن و آلومینیوم | 24 | 3 | 4 | 20 | گواهینامه تایید صلاحیت جوشکار فولادهای S/S و AL طبق استاندارد های ASME,AWS و یاEN |
7 | آموزش جوشکاری در روش(MAG) GMAW روی ورق های فولادی | 48 | 6 | 8 | 40 | گواهینامه تایید صلاحیت جوشکار ورق طبق استاندارد های ASME,AWSو یاEN |
فرآیند های جوشکاری که امکان آموزش عملی آنها در این موسسه یا در محل کارفرما وجود دارد:
فرایند های جوشکاری
- جوشكاري قوس الکترود دستی (SMAW)
- جوشكاري قوس فلز تحت پوشش گاز محافظ (GMAW)
- جوشكاري قوس توپودری (FCAW)
- جوشكاري قوس تنگستن تحت پوشش گاز محافظ (GTAW)
- جوشكاري قوس زير پودري (SAW)
- جوشكاري قوس پلاسما (PAW)
- جوشكاري سرباره الكتريكي (ESW)
- جوشكاري با گاز سوختي و اكسيژن (OFW)
- جوشكاري زائدهاي (SW)
- جوشكاري با پرتو ليزري (LBW)
- جوشكاري با پرتو الكتروني (EBW)
- جوشكاري مقاومتي (RW)
فرآيندهاي لحيمكاري
- لحيمكاري با شعله (TB)
- لحيمكاري كورهاي (FB)
- لحيمكاري القايي (IB)
- لحيمكاري مقاومتي (RB)
- لحيمكاري غوطهوري (DB)
- لحيمكاري مادون قرمز (IRB)
فرآيندهاي برشكاري
- برشكاري با گاز سوختي و اكسيژن (OFC)
- برشكاري با الكترود كربني (CAC-A)
- برشكاري قوسي پلاسما (PAC)
- برشكاري مكانيكي
محتوای دوره آموزش عملی جوشکاری
بخش تئوری کاربردی
- آشنایی با حرفه جوشکاری ، دامنه کاربرد ، اهمیت و جایگاه سازمانی پرسنل جوشکار
- واژه ها و اصطلاحات در جوشکاری طبق AWS A3.0
- آشنایی با نکات ایمنی و سلامت فردی در محیط کارگاه جوشکاری مطابق با استاندارد ANSI Z49.1
- آشنایی با علائم و نقشه خوانی جوش مطابق با استاندارد AWS A2.4
- آشنایی با دستورالعمل های جوشکاری و تاییدیه آنها (WPS/PQR)
- آشنایی با اصول ، متغیر ها و انواع الکترود و سیم جوش
- آشنایی با روشهای برشکاری حرارتی شامل (OFC , PAC )
- آشنایی با آزمایشات جوش شامل تستهای مکانیکی ( مخرب ) و غیر مخرب (NDT)
- آشنایی با عیوب جوش ، علل ، نحوه پیشگیری و تعمیر آنها
بخش کارگاه عملی
- آموزش نحوه آماده سازی لبه ها ( پخ زنی ) و مونتاژ صحیح قطعات طبق نقشه وWPS
- آموزش جوشکاری روی ورق های فولادی برای جوشهای گوشه و نفوذی در وضعیتهای 2G, 3F, 1G , 2F 4G,3G ,
- آموزش جوشکاری روی لوله های فولادی در وضعیتهای 6G,5G, 3G, 2G ,1G ,
- آموزش برشکاری حرارتی ورقهای فولادی با روش های OFC یا PAC
مخاطبین دوره آموزش عملی جوشکاری
جوشکاران ، بازرسین جوش ، دانشجویان و فارغ التحصیلان رشته جوشکاری و سایر رشته های مهندسی، تکنسین های واحد های تولیدی و واحد های تعمیراتی، افرادی که قصد دارند در کمترین زمان ممکن دانش و مهارت فنی جوشکاری را با هدف مهاجرت کسب نمایند.
توانمندیها پس از طی دوره آموزش عملی جوشکاری
- آشنایی با مدارک جوش شامل نقشه خوانی وWPS,PQR
- آشنایی با اصول فرایند، پارامتر های تنظیمی ، الکترود ها ، سیم جوشها ، و سایر مواد مصرفی در روشهای مذکور
- آشنایی با عیوب جوش ، روشهای رفع و تعمیر آنها
- آشنایی با روشهای تست جوش(مخرب و غیر مخرب )
- توانایی و کسب مهارت جوشکاری با روش های مذکور روی ورق هاو لوله ها در وضعیت های تخت ، افقی و عمودی و سقفی
- توانایی و کسب مهارت در عملیات آماده سازی لبه های اتصال و عملیات مونتاژ طبق نقشه و WPS ....
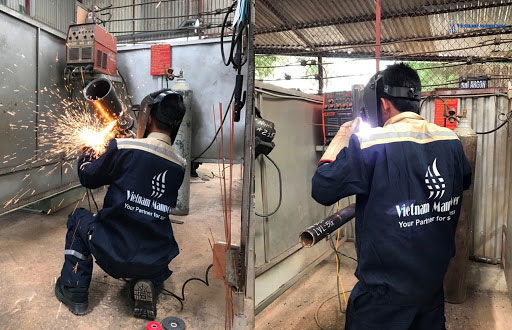
گواهینامه های قابل صدور پس از طی دوره آموزش عملی جوشکاری
به قبول شدگان در آزمونهای نهایی علاوه بر ارائه گواهینامه موفقیت در طی دوره مذکور با ذکر ساعت آموزشی، گواهینامه معتبر تایید صلاحیت جوشکار به صورت جداگانه در روش تحت آموزش بر اساس استانداردهای بین المللی ASME IX ,AWS D1.1 ,ISO 9606 اعطاء خواهد شد. این گواهینامه ها بین المللی بوده و قابلیت ارائه به کلیه شرکت ها و سازمان های داخل و خارج از کشور را دارند. ضمنا علاوه بر موارد فوق، امکان صدور گواهینامه از سازمان آموزش فنی و حرفا ای کشور نیز میسر می باشد. ضمنا مدارکی که فرد پیرو گذراندن دوره در این موسسه، از سازمان آموزش فنی و حرفه ای کشور دریافت میکند، پس ازترجمه و با توجه به دولتی بودن سازمان فنی و حرفه ای، بسیار معتبر بوده و به عنوان یک مدرک قابل ارایه در پروسه مهاجرت استفاده می شود.
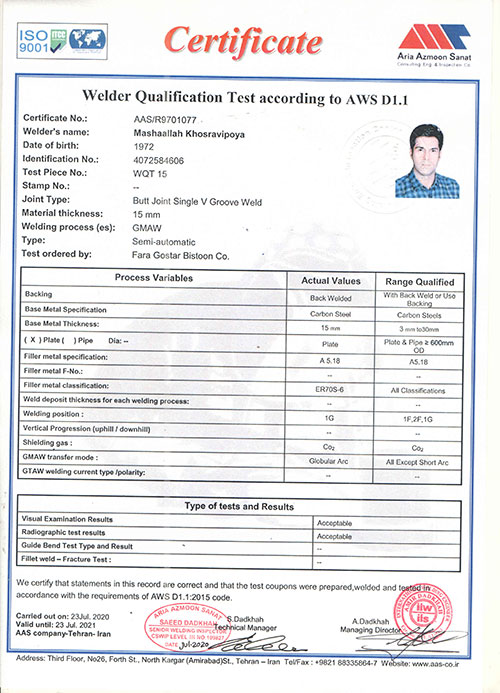
پیش نیاز دوره آموزش عملی جوشکاری
آشنایی مقدماتی با فرآیندهای جوشکاری و برشکاری داشتن تحصیلات حداقل دیپلم و آشنایی به زبان انگلیسی
آشنایی با فرآيندهاي جوشكاري متداول
قبل از توضيح در مورد فرآيندهاي مختلف جوشكاري به تعريف اصطلاح ”جوش“ ميپردازيم. مطابق AWS، جوش عبارت است از اتصال موضعي فلزات يا غير فلزات به يكديگر از طريق اعمال حرارت يا اعمال فشار يا هر دو، با و يا بدون استفاده از فلز پر كننده. در هر فرآيند جوشكاري فاكتورهاي مختلفي در دستيابي به جوش با كيفيت مطلوب، اثر گذار هستند. اين فاكتورها شامل نوع منبع انرژي جهت توليد حرارت، روش محافظت از حوضچه مذاب در برابر اتمسفر و فلز پر كننده (در صورت لزوم) ميباشد. در فرآيندهاي مختلف جوشكاري، فاكتورهاي فوق به طرق متفاوتي محقق ميشوند. فرآيندهاي اتصال و برشكاري متنوعي در توليد قطعات فلزي وجود دارد. اين فرآيندها توسط انجمن جوشكاري آمريكا (AWS) در يك چارت مخصوص طبقه بندي شدهاند. در اين چارت فرآيندهاي اتصال و برشكاري به دو بخش اصلي، شامل فرآيندهاي جوشكاري و فرآيندهاي وابسته تقسيمبندي شدهاند. فرآيندهاي جوشكاري به هفت گروه، شامل جوشكاري قوسي، جوشكاري غير ذوبي (حالت جامد) جوشكاري مقاومتي، جوشكاري با گاز سوختي و اكسيژن، لحيمكاري نرم، لحيمكاري سخت و ساير فرآيندهاي جوشكاري تقسيمبندي شدهاند. فرآيندهاي وابسته شامل فلز پاشي حرارتي، اتصالات چسبي و برشكاري حرارتي ميباشند.
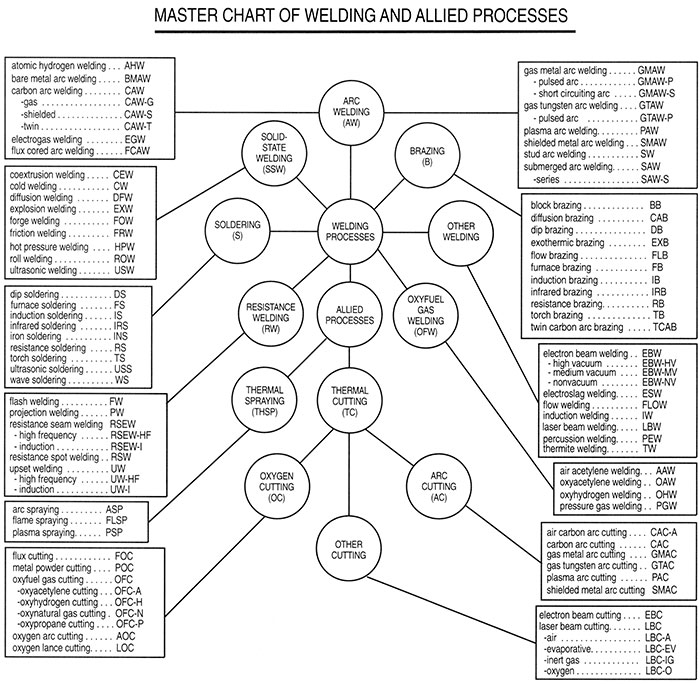
جوشكاري قوس الكترود دستي(SMAW) Shielded Metal Arc Welding
اولين فرآيندي كه در مورد آن توضيح داده ميشود، فرآيند جوشكاري قوس الكترود دستي است. نام ديگر اين فرآيند Stick Welding ميباشد. در اين فرآيند، حرارت از طريق اعمال قوس الكتريكي بين يك الكترود پوششدار و قطعهكار تأمين ميگردد. در شكل ذیل، نماي شماتيك فرآيند SMAW نمايش داده شده است.
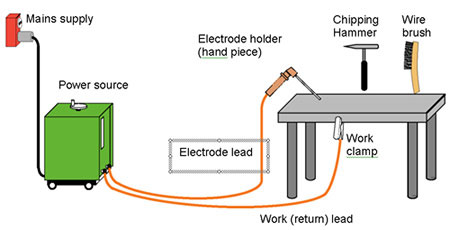
مطابق شكل، يك قوس الكتريكي، بين الكترود و قطعه كار بر قرار شده است. اين قوس الكتريكي، انرژي لازم جهت ذوب فلز پايه، مفتول و روكش الكترود را تأمين ميكند. همزمان با حركت الكترود به سمت راست، فلز جوش پشت سر آن زير پوششي از سرباره (Slag) منجمد ميگردد. به دليل اينكه سرباره نسبت به فلز جوش سبكتر بوده و نقطه ذوب كمتري دارد، روي سطح جوش شناور شده و پس از آن منجمد ميگردد. نكته ديگري كه در شكل نمايش داده شده، گاز محافظي است كه در اثر سوختن روكش الكترود توليد شده است. وظيفه اين گازهاي توليد شده، محافظت قوس و حوضچه مذاب در برابر اتمسفر ميباشد. مهمترين عنصر در فرآيند SMAW، الكترود ميباشد. الكترود از يك مغزي فلزي بهمراه يك روكش (Flux) مخصوص در اطراف آن، تشكيل شده است.
تمام الكترودهاي مخصوص جوشكاري فولادهاي كربني و كم آلياژي، از يك مغزي فولادي يكسان ساخته شده اند. اين مغزي از جنس يك فولاد كم كربن اكسيژن زدائي نشده ميباشد. بنابراين هر عنصر آلياژي ديگر از طريق روكش الكترود به حوضچه مذاب افزوده ميگردد. علت اين امر، اقتصادي بودن تأمين عناصر آلياژي از طريق روكش الكترود ميباشد.
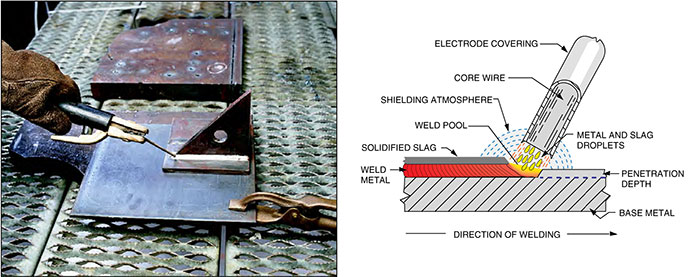
وظايف روكش يا فلاكس الكترود عبارت است از :
1- محافظت (Shielding)
در اثر سوختن روكش الكترود، گازهاي محافظي جهت حفاظت از حوضچه مذاب توليد ميگردد.
2- اكسيژن زدايي (Deoxidation)
روكش الكترود از طريق انجام واكنشهاي شيميايي، اكسيژن و ساير گازهاي جذب شده در حوضچه مذاب را خارج مينمايد.
3- آلياژ سازي (Alloying)
از طريق روكش الكترود، عناصر آلياژي متنوعي به حوضچه مذاب افزوده ميگردد.
4- يونيزاسيون (Ionizing)
عناصر موجود در روكش الكترود به عمليات يونيزاسيون كمك نموده، شروع قوس الكتريكي و پايداري آنرا بهبود ميبخشند.
5- عايق سازي (Insulating)
سرباره منجمد شده روي سطح جوش از طريق ايجاد يك عايق حرارتي سرعت سرد شدن جوش را كاهش ميدهد.
با توجه به اهميت الكترود در فرآيند SMAW، شناسايي و طبقهبندي انواع آن ضروري ميباشد. انجمن جوشكاري آمريكا جهت شناسايي وطبقهبندي اين الكترودها، سيستم معيني تعريف نموده است. اين استاندارد طبقهبندي، جهت فولادهاي كربني AWS A5.1 و جهت فولادهاي كم آلياژي AWS A5.5 ميباشد. بخشهاي مختلف اين سيستم طبقهبندي در شكل نمايش داده شده است. مطابق با اين سيستم طبقهبندي، از يك حرف”E“، بيانگر كلمه Electrode و چهار يا پنج رقم پس از آن استفاده ميشود. دو يا سه رقم اول (در صورتيكه در طبقهبندي از چهار رقم استفاده شده بود، دو رقم اول و در صورتيكه از پنج رقم استفاده شده بود، سه رقم اول) بيانگر حداقل استحكام كششي فلز جوش بر حسب Ksi (كيلو پند بر اينچ مربع) ميباشد. به عنوان مثال در صورتيكه دو رقم اول، عدد ”70“ باشد، بدان معناست كه حداقل استحكام كششي فلز جوش رسوب داده شده 70000Psi ميباشد.
رقم بعدي بيانگر وضعيتي است كه با آن الكترود مجاز به جوشكاري هستيم. عدد ”1“ بيانگر امكان استفاده از الكترود در تمام وضعيتها ميباشد. عدد ”2“ بيانگر سياليت زياد حوضچه مذاب ميباشد، بطوريكه مجاز به استفاده از اين الكترود فقط در وضعيت تخت براي انواع جوشها و وضعيت افقي فقط در جوشهاي نبشي (Fillet) ميباشيم. عدد ”4“، بيانگر مناسب بودن الكترود براي جوشكاري در وضعيت عمودي سرازير ميباشد.
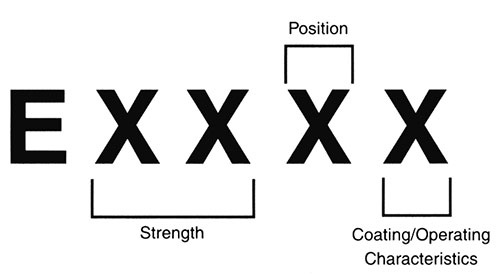
رقم آخر در اين طبقهبندي بيانگر نوع روكش الكترود و نوع جريان و قطبيت پيشنهادي ميباشد. شكل ، رقم آخر را در اين سيستم طبقهبندي نشان ميدهد.
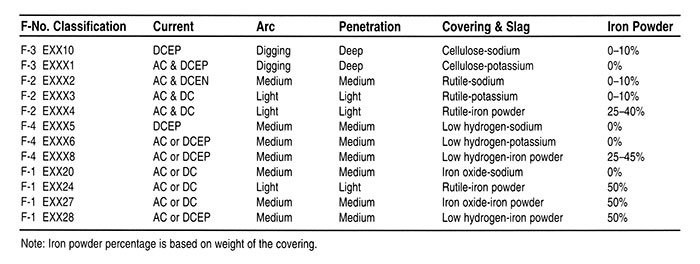
شايان ذكر است كه كليه الكترودهايي كه رقم آخر آنها به ”5“, ”6“ يا ”8“ ختم ميشود، در رده الكترودهاي كم هيدروژن قرار ميگيرند. به منظور حفظ مقدار كم هيدروژن (رطوبت) در اين الكترودها، بايستي آنها را در بستهبنديهاي فلزي مقاوم به رطوبت يا داخل كورههاي مناسب نگهداري نمود. اين كورهها بايد به صورت الكتريكي بوده و قابليت تنظيم درجه حرارت از F°150 تا F°350 را داشته باشند. استفاده از اين كورهها در شرايط استاندارد، مقدار رطوبت را در حداقل مقدار ممكن (كمتر از 2/0 درصد) نگاه ميدارد. پس از بازكردن بستهبندي اين الكترودها، بلافاصله بايد آنها را داخل كوره نگهداري، قرار داد. مطابق با اغلب استانداردها، الكترودهاي كم هيدروژن را بايد بلافاصله پس از خروج از بستهبندي اوليه، داخل كوره با حداقل دماي C°120 نگهداري نمود. اين نكته حائز اهميت است كه قرار دادن ساير الكترودها (غير از الكترودهاي كم هيدروژن) داخل كوره، ممكن است در كارائي موثر آنها اثر سوء داشته باشد. به عنوان مثال بعضي الكترودها طوري ساخته شدهاند كه روكش آنها حاوي مقدار معيني رطوبت باشد. حال در صورت حذف اين رطوبت در كارايي آنها اختلالاتي رخ ميدهد.
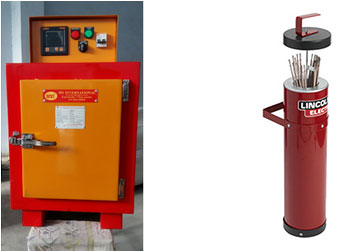
الكترودهاي مخصوص جوشكاري فولادهاي كم آلياژي عموماً بر اساس يك پسوند پس از طبقه بندي ذكر شده فوق، شناسايي ميشوند. اين پسوندها معرف نوع و ميزان عناصر آلياژي در روكش الكترود ميباشند كه در شكل نشان داده شده است.
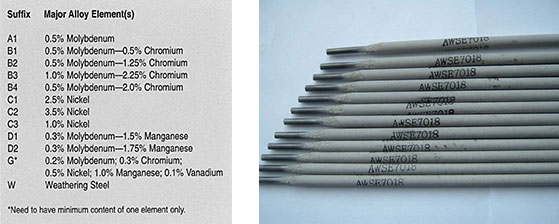
تجهيزات فرآيند SMAW نسبتاً ساده ميباشد. مطابق شكل ، از منبع قدرت، دو كابل خارج شده است. يكي به انبر الكترود گير و ديگري به قطعه كار متصل ميگردد. در اثر ايجاد قوس الكتريكي بين نوك الكترود و قطعه كار، حرارت لازم جهت ذوب تأمين ميشود.
در اين فرآيند از يك منبع قدرت با مشخصات ولت-آمپر جريان ثابت استفاده ميشود. در صورتيكه جوشكار در حين عمليات جوشكاري، طول قوس را افزايش دهد، به دليل افزايش مقاومت قوس، ولتاژ افزايش يافته و شدت جريان كاهش مييابد.

با توجه به اينكه فرآيند SMAW، يك فرآيند قديمي بوده و فرآيندهاي جديدتري ابداع شدهاند ولي هنوز اين روش به عنوان يك فرآيند عمومي جوشكاري در صنايع مختلف مورد استفاده قرار ميگيرد. اين بدان علت است كه تجهيزات آن نسبتاً ساده و ارزان قيمت بوده و به سادگي قابل حمل و نقل ميباشند.
اخيراً منابع قدرتي ساخته شدهاند كه كوچك و سبك بوده و به راحتي توسط جوشكار به محل كار حمل ميشوند. ضمناً با توجه به در دسترس بودن الكترودهاي متنوع جهت مقاصد مختلف، ميتوان به جوش با كيفيت مطلوب دست يافت. يكي از محدوديتهاي اين روش سرعت جوشكاري پايين ميباشد زيرا جوشكار ناچار است پس از مصرف هر الكترود،
عمليات را متوقف كرده و الكترود جديد را جايگزين نمايد. در بسياري از موارد فرآيندهاي جوشكاري اتوماتيك و نيمه اتوماتيك به دليل سرعت بالاتر جايگزين روش SMAW شدهاند. محدوديت ديگر اين روش كه بر سرعت اجراي جوشكاري نيز اثر دارد، اتلاف زمان جهت تميز كاري سرباره در هر پاس ميباشد. همچنين هنگام استفاده از الكترودهاي كم هيدروژن به منظور به حداقل رساندن درصد هيدروژن بايستي آنها را داخل كورههاي مخصوص نگهداري نماييم.
پس از بيان اصول فرآيند SMAW به ذكر چند عيب كه بروز آن در اين فرآيند محتمل است ميپردازيم. مورد اول، ایجاد حفرههاي گازي (Porosity) در جوش ميباشد. دليل بروز حفرات گازي حضور رطوبت يا چربي و آلودگي در موضع جوش ميباشد. رطوبت از طريق روكش الكترود، اتمسفر اطراف محل جوشكاري و چربيها از طريق سطوح آلوده قطعه كار، وارد موضع جوش ميشوند.
يكي ديگر از دلايل بروز حفرات گازي، جوشكاري با طول قوس بلند ميباشد. اين موضوع هنگام جوشكاري با الكترود كم هيدروژن اهميت بالاتري دارد، بنابراين دراين مورد، جوشكاري با طول قوس كوتاه ميتواند به حذف Porosity كمك نمايد. دليل ديگر بروز حفرات گازي پديده وزش قوس (Arc Blow) ميباشد. براي فهم بهتر وزش قوس بايد به اين نكته اشاره نمود كه هرگاه جريان برق از يك هادي عبور كند، يك دسته از خطوط ميدان مغناطيسي به صورت دايرههاي متحدالمركز حول هادي به وجود ميآيد (مطابق شكل). حال هنگام جوشكاري فلزات مغناطيسي نظير فولادهاي كربني، ميدان مغناطيسي به وجود آمده حول الكترود باعث انحراف قوس ميشود
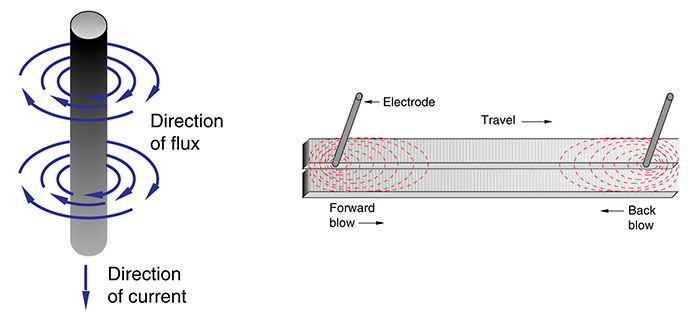
جهت كاهش اثرات وزش قوس راههاي ذيل پيشنهاد ميگردد:
- 1. تغيير جريان از DC به AC
- 2. به حداقل رساندن طول قوس
- 3. كاهش آمپر جوشكاري
- 4. متمايل كردن الكترود به جهتي خلاف جهت وزش قوس
- 5. استفاده از خال جوشهاي بزرگ در دو انتهاي اتصال
- 6. استفاده از تكنيك يك گام به عقب (Back Step)
- 7. انجام جوشكاري، به سمتي كه از قبل جوشكاري شده است.
- 8. جهت پيشرفت جوشكاري به سمت اتصال بدنه صورت گيرد.
- 9. چرخاندن كابل اتصال بدنه به دور قطعه تا اثر ميدان مغناطيسي ايجاد كننده وزش قوس را خنثي كند.
پديده وزش قوس علاوه بر ايجاد حفرات گازي ممكن است سبب جرقه و پاشش، سوختگي كنار جوش، ظاهر نامناسب جوش و عدم ذوب گردد. يكي ديگر از عيوب محتمل در اين فرآيند، حبس سرباره (Slag Inclusion) ميباشد. در صورتيكه به دليل عدم رعايت تكنيك مناسب جوشكاري يا كم بودن شدت جريان، سرباره مذاب نتواند روي سطح مذاب جاري گردد و در لابه لاي جبهههاي انجماد گرفتار شود، اين عيب رخ ميدهد. دليل ديگر بروز اين عيب، عدم تميزكاري مناسب سرباره در بين پاسها ميباشد.
بطوركلي از آنجايي كه روش SMAW به صورت دستي انجام ميشود، احتمال بروز عيوب ديگري از جمله عدم ذوب، عدم نفوذ، ترك، سوختگي كنار جوش، سر رفتن فلز جوش و ظاهر نامناسب جوش امكان پذير ميباشد.
جوشكاري قوس فلزي تحت پوشش گاز محافظ (GMAW) Gas Metal Arc Welding
نام ديگر اين فرآيند (Metal Inert Gas/Metal Active Gas) MIG/MAG ميباشد. كاربري اين روش عموماً به صورت نيمه اتوماتيك ميباشد ولي گاهي اوقات به صورت تمام اتوماتيك نيز مورد استفاده قرار ميگيرد. در اين روش حرارت لازم جهت ذوب، از طريق ايجاد قوس الكتريكي مابين يك الكترود كلافي پيوسته و قطعه كار تأمين ميگردد. الكترود كلافي علاوه بر ايجاد قوس الكتريكي و توليد حرارت، خود ذوب شده و فلز جوش را تأمين مينمايد. شكل نماي شماتيك فرآيند GMAW را نشان ميدهد. قوس و منطقه مذاب بواسطه يك گاز محافظ كه از طريق تورچ جوشكاري هدايت ميگردد، محافظت ميشوند. گاز مورد استفاده ممكن است خنثي و يا فعال باشد. در اين فرآيند از گازهاي آرگن، هليوم و مخلوط اين دو گاز به عنوان گازهاي خنثي، عموماً جهت جوشكاري فلزات غيرآهني استفاده ميگردد. از گازهاي دي اكسيد كربن، مخلوط آرگن و CO2 و مخلوط آرگن و اكسيژن به عنوان گازهاي فعال جهت جوشكاري فلزات آهني (فولادها) استفاده ميشود.
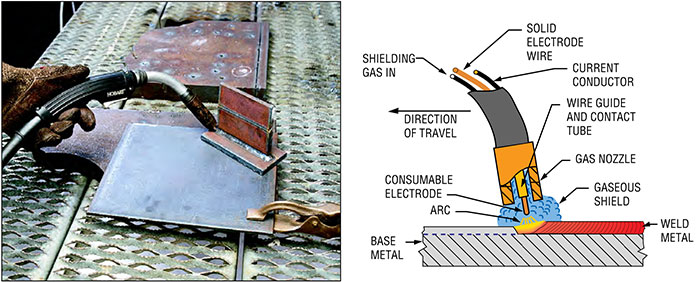
طبقهبندي الكترودهاي كلافي در روش GMAW جهت فولادهاي كربني مطابق با استاندارد AWS A5.18 در شكل نشان داده شده است. ”ER“ بيانگر اين موضوع است كه اين طبقه بندي هم جهت الكترودهاي كلافي و هم جهت سيم جوش در فرآيندهاي ديگر قابل استفاده ميباشد (در صورتي كه فلز پر كننده، هادي جريان برق باشد به عنوان الكترود و در غير اينصورت سيم جوش تلقي ميشود). دو يا سه رقم بعد از آن بيانگر حداقل استحكام كششي فلز جوش بر مبناي ksi ميباشد. حرف ”S“ بيانگر اين است كه الكترود به صورت توپر (Solid) ميباشد. در نهايت عدد پس از خط تيره بيانگر تركيب شيميايي الكترود ميباشد. اين عدد معمولاً بيانگر درصد عناصر اكسيژن زدا از قبيل Al,Mn,Si در الكترود ميباشد. اين عناصر از بروز حفرات گازي در جوش جلوگيري ميكنند.
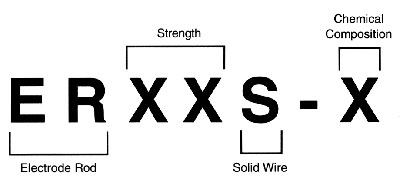
به دليل عدم وجود فلاكس در اين فرآيند، نگهداري مناسب الكترود در زمان عدم استفاده، از اهميت ويژهاي برخوردار است. بنابراين اين الكترودها بايد تميز و در محيطي عاري از ذرات گرد و غبار، چربي، رطوبت و ساير آلودگيهاي موجود در اتمسفر، نگهداري شوند. بهترين روش نگهداري الكترود، در بسته بنديهاي پلاستيكي اوليه ميباشد. همچنين زمانيكه كلاف الكترود را از بسته بندي اوليه خارج و در سيستم تغذيه دستگاه قرار ميدهيم، در صورتيكه براي مدت زمان طولاني قصد استفاده از دستگاه را نداريم، بايد توسط پوشش مناسبي، آن را نگهداري نماييم. منبع قدرت مورد استفاده در فرآيند GMAW از نوع ولتاژ ثابت (Constant Voltage) بوده و در اين فرآيند عموماً از جريان مستقيم و الكترود مثبت (DCEP) استفاده ميگردد.
فرآيند GMAW در شكل ذیل نمايش داده شده است. همانطور كه مشاهده ميكنيد تجهيزات اين فرآيند نسبت به فرآيند SMAW، پيچيدهتر ميباشند. تجهيزات شامل يك منبع قدرت، سيستم تغذيه الكترود، كپسول گاز و تورچ جوشكاري ميباشد. وظيفه تورچ، هدايت الكترود و گاز محافظ به محل جوشكاري است. جوشكار، ولتاژ را از روي منبع قدرت و سرعت تغذيه الكترود را از روي سيستم تغذيه تنظيم مينمايد. در اين فرآيند با افزايش سرعت تغذيه الكترود، شدت جريان نيز افزايش مييابد. همچنين نرخ ذوب الكترود با شدت جريان رابطه مستقيم دارد.
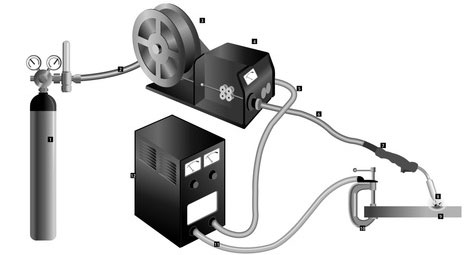
در فرآيند GMAW چهار مدل مختلف انتقال فلز با توجه به تنظيمات دستگاه وجود دارد. اين مدلها عبارتند از :
- اتصال كوتاه يا قوس كوتاه (Short Circuiting)
- اسپري يا پاششي (Spray)
- قطرهاي (Globular)
- پالسي يا ضرباني (Pulse)
منظور از مدل انتقال فلز، نحوه جدا شدن قطرات مذاب از نوك الكترود و انتقال آنها به حوضچه مذاب ميباشد. شكل ذیل، مدلهای انتقال فلز را نمايش ميدهد. هر كدام از مدلهاي انتقال فلز مشخصات متفاوتي دارند بطوريكه ميتوان هر يك از آنها را به عنوان يك فرآيند جوشكاري متفاوت تلقي نمود. همچنين هر كدام مزايا و محدوديتهاي ويژهاي دارند و جهت كاربردهاي مخصوص مورد استفاده قرار ميگيرند. مدل انتقال فلز به فاكتورهايي از قبيل ميزان ولتاژ و شدت جريان، نوع گاز محافظ مورد استفاده و مشخصات منبع قدرت بستگي دارد. يكي از وجوه تمايز بين مدلهاي فوق، اختلاف در ميزان حرارت ورودي به قطعه كار ميباشد. قوس اسپري بيشترين حرارت ورودي را ايجاد ميكند، پس از آن قوس پالس، قوس قطرهاي و در نهايت قوس كوتاه. بنابراين انتخاب قوس اسپري جهت جوشكاري مقاطع ضخيم با سرعت بالا مناسب ترين انتخاب ميباشد، اگرچه با اين قوس امكان جوشكاري فقط در وضعيت تخت ميسر است. قوس قطرهاي از ثبات كمتري برخوردار بوده و جرقه و پاشش زيادي دارد. امكان دستيابي به قوس پالسي فقط توسط دستگاههايي كه مجهز به توليد جريان خروجي ضرباني باشند، ميسر است. در اين سيستم، انرژي قوس الكتريكي بين دو سطح شدت جريان تحتاني و فوقاني كه مقادير آنها روي دستگاه قابل تنظيم ميباشد، تغيير مييابد. اين موضوع سبب كنترل بهتر حرارت ورودي ميگردد. قوس كوتاه كمترين ميزان حرارت ورودي را ايجاد مينمايد، بنابراين مناسبترين مدل انتقال فلز جهت جوشكاري قطعات نازك و گپهاي زياد حاصل از عمليات مونتاژ نامناسب ميباشد. در قوس كوتاه، قطره مذاب قبل از جدا شدن كامل از نوك الكترود، سطح حوضچه مذاب را لمس ميكند. امكان جوشكاري با قوس كوتاه در تمام وضعيتها ميسر است. هنگام جوشكاي مقاطع ضخيم، به دليل كم بودن ميزان انرژي قوس كوتاه، احتمال بروز ذوب ناقص (LOF) زياد ميباشد. همانطوركه قبلاً نيز اشاره شد، گاز محافظ تأثير بسزايي بر نوع انتقال فلز دارد. به عنوان مثال قوس اسپري فقط هنگامي كه حداقل 80 درصد آرگن در مخلوط گاز محافظ باشد، ايجاد ميشود. علت متداول بودن گاز CO2 در فرآيند GMAW جهت فولادهاي كربني، ارزان بودن و نفوذ جوش مطلوب آن ميباشد. با اين حال استفاده از اين گاز سبب افزايش جرقه و پاشش و اتلاف زمان جهت تميزكاري ميگردد.
فرآيند GMAW به طور گستردهاي جهت جوشكاري فلزات آهني و غيرآهني به كار ميرود. استفاده از گاز محافظ به جاي فلاكس كه قابليت جذب رطوبت دارد، درصد هيدروژن را درناحيه جوش و HAZ كاهش داده و اين فرآيند را به عنوان يك فرآيند كم هيدروژن مطرح ميسازد. همچنين به دليل عدم وجود سرباره روي جوش و عدم نياز به تميزكاري، استفاده از اين فرآيند جهت كاربردهاي اتوماتيك و رباتيك مناسب ميباشد. با اين فرآيند امكان جوشكاري به صورت پيوسته و با حداقل نقاط Stop-Start ميسر ميباشد. اين موضوع علاوه بر افزايش سرعت جوشكاري، نقاط ضعيف و معيوب را به حداقل ميرساند. از مزاياي ديگر اين روش، نرخ رسوب زياد فلز جوش ميباشد كه موجب كاهش هزينهها ميگردد. در اين فرآيند به دليل عدم وجود فلاكس ميزان دود توليد شده در حين جوشكاري در مقايسه با فرآيندهاي SMAW و FCAW كمتر ميباشد. اين موضوع از ديدگاه تهويه محيط جوشكاري حايز اهميت است. كمتر بودن ميزان دود و عدم وجود سرباره در حين جوشكاري قابليت رويت و كنترل حوضچه مذاب را براي جوشكار آسانتر ميسازد. از محدوديتهاي اين روش، حساس بودن فرآيند به وزش باد و انحراف چتر گاز محافظ از حوضچه مذاب ميباشد. بنابراين استفاده از اين فرآيند در محيطهاي باز پيشنهاد نميگردد.
دبي گاز محافظ با توجه به حجم حوضچه مذاب و سايز نازل گاز تنظيم ميشود. دبي گاز بيش از اندازه، سبب ايجاد اغتشاش در جريان گاز ميگردد. اغتشاش در گاز محافظ سبب هدايت گازهاي موجود در اتمسفر به حوضچه مذاب شده و منجر به توليد حفرات گازي در حوضچه جوش ميشود. از محدوديتهاي ديگر اين فرآيند پيچيدهتر بودن تجهيزات در مقايسه با فرآيند SMAW ميباشد. به عنوان مثال در صورت معيوب بودن نازل تماس يا فنر هدايت كننده الكترود، عملكرد فرآيند دچار خدشه شده و نتيجه آن، ايجاد جوش معيوب ميباشد.
عيوب متداولي كه در فرآيند GMAW محتمل ميباشند عبارتند از: حفرات گازي به دليل آلودگي سطح قطعه يا الكترود، عدم ذوب مخصوصاً هنگام جوشكاري با قوس كوتاه روي قطعات ضخيم، عدم ثبات قوس و تلاطم حوضچه مذاب به دليل معيوب بودن نازل تماس و فنر هدايتكننده الكترود. با رعايت بعضي نكات، عيوب مذكور به سادگي قابل پيشگيري هستند. جهت كاهش بروز حفرات گازي بايستي قبل از جوشكاري، سطح قطعات را تميزكاري كرده و منطقه جوشكاري را از وزش باد محافظت نمـود. همچـنين بايـد گاز محافظ را از نظر عدم وجود ناخالصي يا رطوبت بيش از اندازه بررسي نمود. ميتوان با افزايش انرژي قوس، هدايت مناسب تورچ روي ديوارههاي اتصال و تميزكردن لايههاي اكسيدي در هر پاس، عيب عدم ذوب را كاهش داد.
در نهايت به منظور جلوگيري از عيوب مربوط به عدم تغذيه يكنواخت الكترود به حوضچه مذاب لازم است از سالم بودن نازل تماس اطمينان حاصل نمود. با توجه به حجم جوشكاري، نازل تماس بايد به صورت منظم تعويض گردد زيرا در اثر عبور الكترود، علاوه بر بزرگ شدن سايز سوراخ، روي ديوارههاي داخلي آن خش ايجاد ميشود و اين موضوع برق رساني به الكترود را دچار خدشه ميكند. توصيه ميشود پس از هر بار تعويض كلاف الكترود، فنر هادي الكترود را خارج نموده و با عبور هواي فشرده، آن را تميز كاري نمود. اين موضوع سبب خارج شدن ذرات گرد و غبار ميگردد.
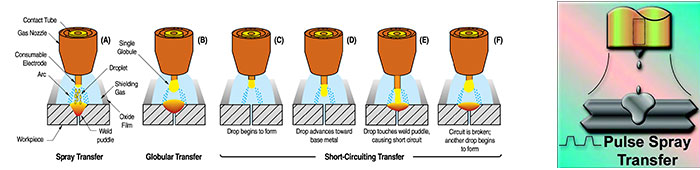
جوشكاري قوس تو پودري (FCAW) Flux Cored Arc Welding
اين فرآيند مشابه فرآيند GMAW ميباشد با اين تفاوت كه در فرآيند FCAW از يك الكترود لولهاي (Tubular) كه داخل آن از پودر پر شده است استفاده ميشود. شكل ذیل، فرآيند FCAW از نوع خود محافظ (Self Shield) را نمايش ميدهد مطابق شكل، يك قوس الكتريكي بين الكترود لوله اي و قطعه كار برقرار شده كه حوضچه مذاب را تشكيل ميدهد. از طرفي پس از انجماد، يك لايه سرباره (Slag) روي سطح جوش مشاهده ميگردد، در اين فرآيند با توجه به مشخصات الكترود مورد استفاده، امكان جوشكاري با گاز محافظ و يا بدون آن ميسر ميباشد.
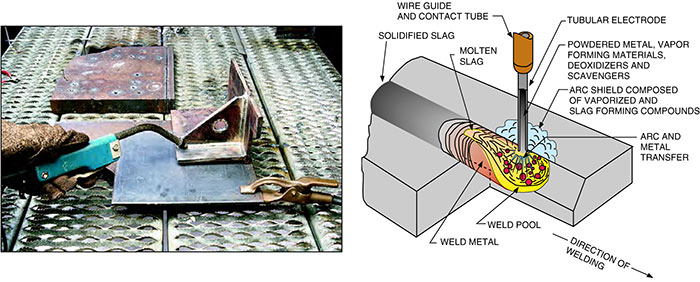
بعضي الكترودها طوري طراحي شدهاند كه گاز توليد شده ناشي از سوختن فلاكس، جهت محافظت از حوضچه جوش كافي ميباشد. اين الكترودها به الكترودهاي خود محافظ (Self Shield) موسوم هستند و برخي ديگر از الكترودها علاوه بر فلاكس، به يك گاز محافظ خارجي نيازمند هستند، به اين الكترودها (Gas Shield) ميگويند. با توجه به شكل ذیل، مطابق با استاندارد AWS A5.20، يك سيستم طبقهبندي معين، جهت الكترودهاي فرآيند FCAW تعريف شده است. حرف ”E “ بيانگر الكترود ميباشد. اولين رقم پس از E بيانگر استحكام كششي فلز جوش رسوب داده شده بر حسب ده هزار پند بر اينچ مربع ميباشد.
به عنوان مثال رقم ”7“ بيانگر 70000Psi استحكام كششي فلز جوش ميباشد. رقم دوم كه يكي از اعداد ”0“ و يا ”1“ است بيانگر وضعيت جوشكاري ميباشد. ”0“ بيانگر مناسب بودن الكترود فقط در وضعيتهاي تخت و افقي در جوشهاي Fillet (2F,1F,1G)و ”1“ بيانگر قابل استفاده بودن الكترود در تمام وضعيتها ميباشد. حرف ”T“ بيانگر لولهاي (Tubular) بودن الكترود ميباشد. عدد پس از خط تيره، بيانگر فاكتورهايي از قبيل تركيب شيميايي فلز جوش رسوب داده شده، نوع جريان و قطبيت قابل استفاده و نياز يا عدم نياز به گاز محافظ ميباشد.
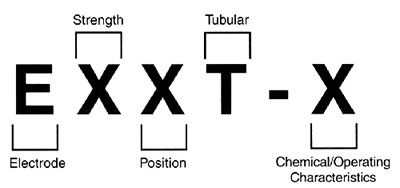
از ديدگاه بازرسي جوش، آگاه بودن نسبت به نياز يا عدم نياز به گاز محافظ در فرآيند FCAW از اهميت ويژهاي برخوردار است. بعضي الكترودها از تركيباتي ساخته شدهاند كه گاز ناشي از سوختن فلاكس جهت محافظت حوضچه مذاب كافي ميباشد. اين الكترودها با پسوندهاي 14,13,11,10,8,7,6,4,3 طبقهبندي ميشوند. برخي ديگر از الكترودها طوري طراحي شدهاند كه علاوه بر فلاكس به يك گاز محافظ خارجي جهت محافظت حوضچه مذاب نياز دارند اين الكترودها با پسوندهاي 12,9,5,2,1 طبقهبندي ميشوند. منبع قدرت در فرآيند FCAW همانند فرآيند GMAW، ولتاژ ثابت ميباشد. با توجه به طبقهبندي الكترودها در صورتيكه رقم پسوند يكي از اعداد (12,9,6,4,3,2,1) باشد از جريان DCEP و در صورتيكه (14,13,11,10,8,7) باشد از DCEN استفاده ميشود. در صورتيكه رقم پسوند عدد (5) باشد DCEN و DCEP هر دو قابل استفاده هستند.
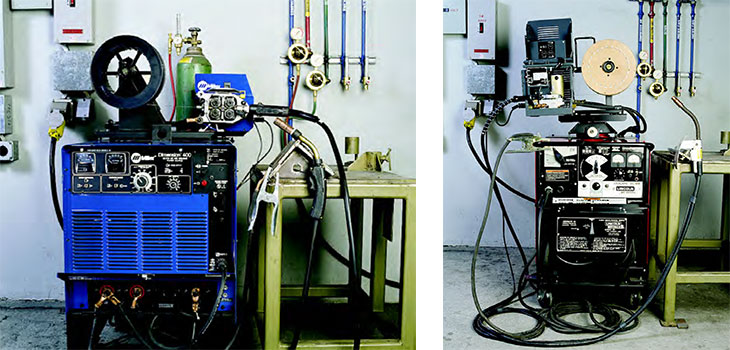
حساسيت كمتر فرآيند FCAW نسبت به جوشكاري روي سطوح آلوده و نرخ رسوب بالاتر در اين فرآيند، آنرا در بسياري از كاربردها جايگزين مناسبي جهت فرآيندهاي SMAW و GMAW نموده است. استفاده از اين فرآيند هم داخل كارگاه و هم در فضاي باز نتايج مطلوبي به همراه دارد. اين فرآيند اغلب جهت فلزات آهني شامل فولادهاي كربني و فولادهاي ضد زنگ به كار ميرود. بعضي از الكترودهاي مخصوص فولادهاي ضدزنگ از يك تيوب فولاد كربني ساخته شدهاند كه داخل آن پودر حاوي عناصر آلياژي كرم، نيكل و غيره قرار دارد.
فرآيند FCAW به دليل مزاياي بسيار، كاربرد گستردهاي پيدا كرده است. نرخ رسوب در اين فرآيند زياد ميباشد بدين معنا كه مقدار فلز جوش رسوب داده شده در واحد زمان زياد ميباشد. از طرفي به دليل زياد بودن ميزان انرژي قوس، نفوذ جوش افزايش يافته و احتمال بروز عيب عدم ذوب كاهش مييابد. به دليل نيمه اتوماتيك بودن فرآيند، جوشكار به مهارت كمتري نياز دارد. همچنين به دليل پيوسته بودن تغذيه الكترود نياز به اتلاف وقت جهت تعويض الكترود وجود ندارد.
به دليل وجود فلاكس، حساسيت اين فرآيند نسبت به آلودگيهاي سطح قطعه كار در مقايسه با فرآيند GMAW كمتر است و نيز به همين دليل پس از جوشكاري يك لايه سرباره روي سطح جوش قرار خواهد گرفت كه منجر به كاهش سرعت سرد شدن ميگردد. فرآيند FCAW محدوديتهايي دارد كه بازرس جوش بايد نسبت به آنها آگاهي كافي داشته باشد.
سرباره تشكيل شده روي سطح جوش، بايستي قبل از رسوب پاسهاي بعدي همچنين قبل از اجراي بازرسي چشمي تميزكاري شود. به دليل وجود فلاكس در حين جوشكاري، مقدار قابل توجهي دود توليد ميشود كه نياز به تهويه مناسب دارد. از طرفي دودهاي توليد شده در محل جوشكاري مانع رؤيت كامل حوضچه مذاب و كنترل بهينه آن توسط جوشكار ميگردد. تجهيزات اين فرآيند در مقايسه با فرآيند SMAW پيچيدهتر بوده و هزينههاي اوليه تجهيز بيشتر ميباشد.
عيوب متداول در اين روش عبارتند از: سرباره حبس شده (Slag Inclusion) كه به دلايل مختلف از جمله عدم تميزكاري مناسب بين پاسها و استفاده از تكنيك نامناسب جوشكاري رخ ميدهد.
در اين فرآيند، رعايت سرعت مناسب جوشكاري اهميت ويژهاي دارد بطوريكه همواره بايد قوس الكتريكي به سمت لبه جلويي حوضچه مذاب متمركز باشد. در صورتيكه سرعت جوشكاري خيلي كند باشد، قوس به سمت مركز حوضچه مذاب يا روي لبه پشتي آن متمركز شده كه اين سبب جلو افتادن سرباره مذاب و حبس آن ميگردد. مشكل بعدي، عدم تغذيه يكنواخت الكترود به حوضچه مذاب است كه عيوبي را به دنبال خواهد داشت. اين مشكل به دليل معيوب بودن تجهيزات و عدم تعمير و نگهداري مناسب آن ميباشد. در اين فرآيند عيوب ديگري نيز از قبيل حفرههاي گازي، عدم ذوب و عدم نفوذ رخ ميدهند.
جوشكاري قوس تنگستن تحت پوشش گاز محافظ(GTAW) Gas Tungsten Arc Welding
شكل ذیل، نماي شماتيك فرآيند GTAW را نمايش ميدهد. در اين فرآيند حرارت لازم جهت ذوب از طريق تشكيل قوس الكتريكي بين يك الكترود غير مصرفي از جنس تنگستن يا آلياژ آن و قطعه كار تأمين ميگردد. نام دیگر این روشTIG میباشد.

در صورت نياز، فلز پر كننده عموماً به صورت دستي يا گاهي اوقات به صورت اتوماتيك به حوضچه مذاب تزريق ميشود. حوضچه مذاب، سيم جوش و قوس الكتريكي به واسطة يك گاز محافظ خنثي كه از طريق نازل گاز هدايت ميشود، محافظت ميگردند. به دليل عدم وجود فلاكس، فلز جوش رسوب داده شده عاري از سرباره بوده و نياز به تميزكاري ندارد.
مطابق با استاندارد AWS A5.12 يك سيستم طبقهبندي، جهت الكترودهاي تنگستني تعريف شده است. حرف ”E“ بيانگر كلمه الكترود ميباشد. حرف ”W“ بيانگر كلمه ولفرام يا تنگستن است. پس از W از يك سري حروف و اعداد استفاده ميشود كه بيانگر مقدار و نوع عناصر آلياژي موجود در الكترود تنگستن ميباشند. مطابق با اين استاندارد پنج كلاس الكترود تنگستن معرفي شده، كه هر يك با رنگ مخصوصي مشخص ميشوند.
رنگ | عنصر آلياژي | كلاس |
---|---|---|
ته سبز | تنگستن خالص | EWP |
ته نارنجي | 2.2- 1.8 درصد سريم | EWCe-2 |
ته مشكي | 1 درصد لانتانيوم | EWLa-1 |
ته طلايي | 1.5 درصد لانتانيوم | EWLa-1.5 |
ته آبي | 2 درصد لانتانيوم | EWLa-2 |
ته زرد | 1.2- 0.8 درصد توريم | EWTh-1 |
ته قرمز | 2.2-1.7 درصد توريم | EWTh-2 |
ته قهوهاي | 0.4-0.15 درصد زيركونيوم | EWZr |
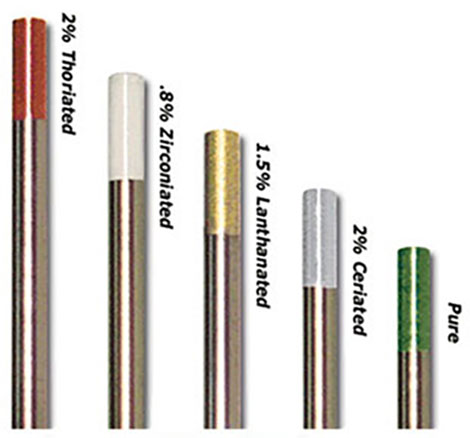
حضور عناصري از قبيل توريم يا زيركونيوم در الكترود تنگستن سبب سهولت در خروج الكترونها از نوك الكترود ميگردد. اين موضوع سبب سهولت در شروع و پايداري قوس الكتريكي در حين جوشكاري ميشود.
الكترودهاي تنگستن خالص (EWP) به دليل قابليت كروي شدن نوك آنها هنگام اعمال حرارت، اغلب جهت جوشكاري آلومينيوم مورد استفاده قرار ميگيرند. با توجه به اينكه آلومينيوم با جريان AC جوشكاري ميشود و تحت اين جريان حدود 50 درصد حرارت در نوك الكترود تمركز دارد، كروي بودن نوك الكترود به كاهش تمركز جريان و جلوگيري از آسيب به الكترود كمك مينمايد. الكترود EWTh-2 اغلب جهت جوشكاري فلزات آهني مورد استفاده قرار ميگيرد.طبقهبندي سيم جوش در فرآيند GTAW با پيشوند ER شروع ميشود. اين طبقهبندي جهت فولادهاي كربني توسط استانداردAWS A5.18 مطرح شده است. طول سيم جوشها معمولاً 36 اينچ بوده و مشخصه سيم جوش در انتهاي آن حك شده است.
فرآيند GTAW با جريانهاي DCEN، DCEP و AC قابل استفاده ميباشد. با جريان DCEP، تمركز حرارت در الكترود و با جريان DCEN تمركز آن در قطعه كار ميباشد. در جريان AC، حرارت به صورت يكسان در الكترود و قطعه توزيع ميگردد. از جريان AC به دليل عمليات اكسيدزدايي آن جهت جوشكاري آلومينيوم و منيزيم استفاده ميشود. جريان DCEN تقريباً براي تمام فلزات غير از آلومينيوم و منيزيم قابل استفاده ميباشد. شكل ذیل تأثير نوع جريان و قطبيت بروي نفوذ جوش، عمليات اكسيدزدايي، توزيع حرارت در الكترود و قطعه كار و ظرفيت حمل جريان را نمايش ميدهد. در اين فرآيند از يك گاز خنثي جهت محافظت حوضچه مذاب استفاده ميشود. گازهاي خنثي با فلز تركيب نشده و عمليات محافظت را به خوبي انجام ميدهند. آرگن و هليوم دو گاز متداول مورد استفاده در فرآيند GTAW هستند. گاهي اوقات در جوشكاري فولادهاي ضدزنگ اندكي هيدروژن به گاز آرگن افزوده ميشود. هيدروژن حوضچه مذاب را احياء نموده و جوش تميزي ايجاد ميكند. در اين فرآيند از منبع قدرت جريان ثابت مشابه فرآيند SMAW استفاده ميشود.
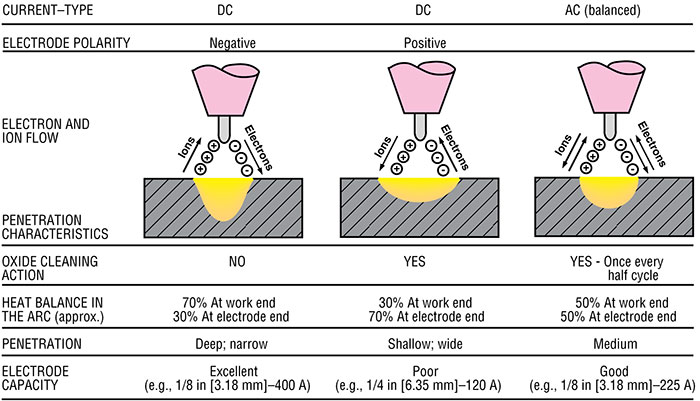
شكل ذیل تجهيزات فرآيند GTAW را نمايش ميدهد. در اغلب دستگاهها از يك مولد فركانس بالا جهت كمك به شروع قوس الكتريكي استفاده ميگردد. به منظور كنترل درجه حرارت در حين جوشكاري، از يك ريموت كنترل قابل تنظيم روي تورچ يا از يك پدال پايي استفاده ميشود. استفاده از ريموت كنترل، هنگام جوشكاري ورقهاي نازك يا جوشكاري پاس ريشه لولهها بسيار مفيد ميباشد. اين فرآيند كاربردهاي گستردهاي در صنعت دارد و قابل استفاده جهت تمام فلزات جوش پذير ميباشد. قابليت ثبات قوس مطلوب اين فرآيند، در آمپراژ پايين، امكان جوشكاري قطعات نازك (زير 1mm) را فراهم نموده است. به دليل كيفيت جوش مطلوب و قابل كنترل بودن فرآيند، ميتوان از آن در صنايع خاص، از جمله صنايع هواپيمايي، صنايع غذايي و دارويي، صنايع پتروشيمي و نيروگاهي استفاده نمود. از مزاياي عمده اين فرآيند، كيفيت بالا و ظاهر مناسب جوش ميباشد. همچنين به دليل عدم وجود فلاكس، به تميزكاري سرباره پس از جوشكاري نيازي نيست. همانطور كه قبلاً اشاره شد امكان جوشكاري قطعات خيلي نازك ميسر ميباشد. ضمناٌ به دليل طبيعت اين فرآيند كه منبع حرارت، مجزا از فلز پركننده ميباشد، قابليت جوشكاري آلياژها يا قطعاتي كه با فرآيندهاي ديگر به سختي جوشكاري ميشوند، وجود دارد
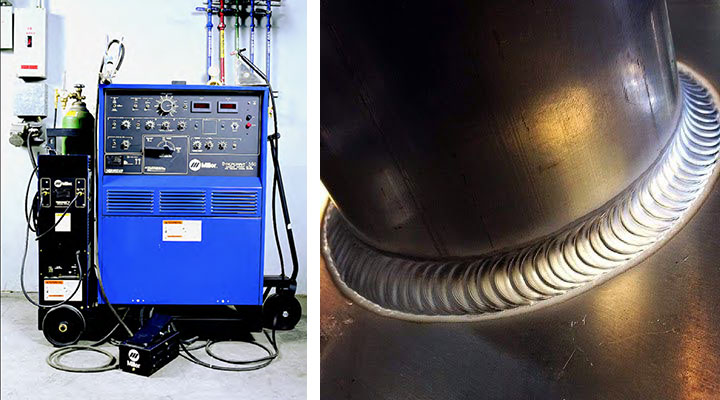
گاهي اوقات با توجه به طرح اتصال، نيازي به افزودن سيم جوش نيست. زماني كه براي يك آلياژ مشخص، سيم جوش در دسترس نباشد ميتوان يك باريكه نازك از فلز پايه را برش داده و به عنوان سيم جوش مورد استفاده قرار داد.
در كنار اين مزايا، محدوديتهايي در اين فرآيند وجود دارد. فرآيند GTAW جزء كندترين فرآيندهاي جوشكاري محسوب ميشود. به دليل عدم وجود فلاكس، اين فرآيند به تميزي سطوح اتصال و سيم جوش، حساسيت بيشتري دارد. بنابراين حتماً بايستي سطوح اتصال و سيم جوش را قبل از شروع جوشكاري كاملاً تميزكاري نمود. در اين فرآيند مهارت اپراتور اهميت ويژهاي دارد، زيرا كنترل تورچ با يك دست و تغذيه سيم جوش بادست ديگر انجام ميشود.
يكي از عيوب متداول در اين فرآيند، حفرات گازي ميباشد. همانطوركه اشاره شد در صورت وجود مختصري آلودگي روي سطوح قطعه كار يا سيم جوش و يا در گاز محافظ، نتيجه آن، بروز حفرات گازي در فلز جوش خواهد بود.
عيب ديگري كه تقريباً منحصر به فرآيند GTAW است، ناخالصي تنگستن (Tungsten Inclusion) ميباشد. ناخالصي تنگستن در فلز جوش به دلايل متفاوتي ايجاد ميشود. اين دلايل عبارتند از:
- 1- تماس نوك الكترود تنگستن با حوضچه مذاب.
- 2- تماس سيم جوش با نوك الكترود تنگستن در حين جوشكاري.
- 3- آلوده شدن نوك الكترود تنگستن بوسيله جرقه و پاشش.
- 4- عبور دادن جريان زياد از يك الكترود نازك يا الكترودي كه نوك آن بيش از حد، تيز شده است.
- 5- بيرون بودن بيش از اندازه الكترود از كلت (Collet) كه موجب داغ شدن زياد آن ميشود.
- 6- تماس نامناسب الكترود تنگستن با كلت.
- 7- دبي گاز محافظ خيلي كم يا وزش باد كه نتيجه آن، اكسيداسيون الكترود تنگستن داغ ميباشد.
- 8- استفاده از الكترود تنگستن نامرغوب يا تركدار.
- 9- استفاده از گاز محافظ نا مناسب.
- 10- عدم تيز كردن مناسب نوك الكترود.
جوشكاري قوس زير پودري (SAW) Submerged Arc Welding
در اين فرآيند حرارت لازم جهت ذوب از طريق قوس الكتريكي بين يك الكترود كلافي و قطعه كار، زير باراني از پودر (فلاكس) تأمين ميگردد. اين فرآيند به صورت اتوماتيك بوده و اجراي جوشكاري بصورت پيوسته خواهد بود. فرآيند SAW، بيشترين نرخ رسوب را در مقايسه با ساير فرآيندهاي اشاره شده دارا ميباشد. شكل ذیل نماي شماتيك اين فرآيند را نمايش ميدهد. همانطور كه اشاره شده الكترودكلافي از طريق يك سيستم تغذيه همانند فرآيندهاي FCAW وGMAW به حوضچه مذاب تزريق ميشود. اختلاف اصلي، در نحوه محافظت از حوضچه مذاب ميباشد. در فرآيند SAW پودر (فلاكس) از طريق نازلهاي مخصوص به جلوي الكترود يا اطراف آن هدايت ميشود.
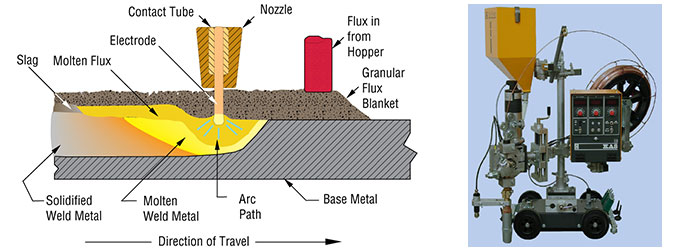
همزمان با حركت تراك و انجام جوشكاري، يك لايه از سرباره منجمد شده و مقاديري فلاكس ذوب نشده، روي سطح جوش را ميپوشانند. پس از هر پاس جوشكاري ميبايستي سرباره را جداسازي نمود. فلاكسهاي ذوب نشده عموماً قابل استفاده مجدد ميباشند. البته براي بعضي كاربردهاي حساس كه تميز بودن فلاكس از اهميت خاصي برخوردار است، استفاده مجدد از آنها پيشنهاد نميشود.
از آنجايي كه در اين فرآيند، فلاكس والكترود به صورت جداگانه استفاده ميشوند، بنابراين ميتوان از تركيبات متنوع فلاكس - الكترود بهره جست. دو نوع اصلي تركيب فلاكس و الكترود جهت دستيابي به فلز جوش آلياژي عبارتند از:
- 1- استفاده از يك الكترود آلياژي با يك فلاكس خنثي.
- 2- استفاده از يك الكترود از جنس فولاد نرم(Mild Steel) به همراه يك فلاكس آلياژي.
در شكل ذیل مطابق با استاندارد AWS A5.17 طبقهبندي فلاكس/ الكترود جهت جوشكاري فولادهاي كربني معرفي شده و به همراه آن 2 مثال ذكر گرديده است.
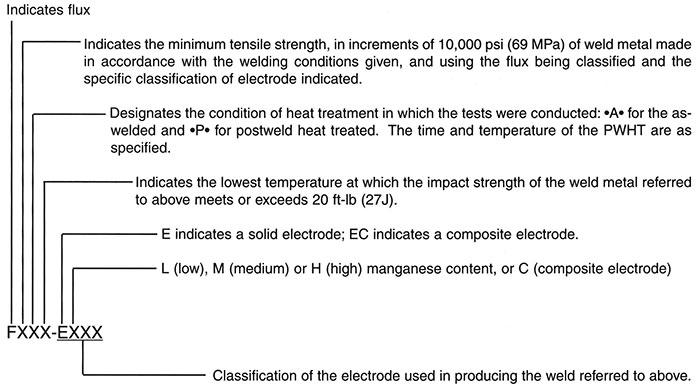
مثال 1) در مورد طبقه بندي F7A6-EMI2K، F7A6 بيانگر فلاكسي ميباشدكه در صورت استفاده با الكترود EMI2K، در شرايط بدون نياز به عمليات حرارتي، فلز جوشي با حداقل استحكام كششي 70000 psi تأمين مينمايد. همچنين در دماي F°-60، حداقل مقاومت به ضربه 27J را تأمين خواهد كرد.
مثال 2) در مورد طبقه بندي F7A4-EC1، F7A4 بيانگر فلاكسي است كه در صورت استفاده با الكترود EC1، در شرايط بدون نياز به عمليات حرارتي (As Welded) فلز جوشي با حداقل استحكام كششي 70000 psi تأمين نموده و در دماي F°-40، داراي حداقل مقاومت به ضربه 27J است.
مطابق شكل ذیل، تجهيزات فرآيند SAW از قسمتهاي مختلفي تشكيل شده است. در اين فرآيند غالباً از يك مولد قدرت ولتاژ ثابت استفاده ميشود. مشابه فرآيندهاي GMAW و FCAW، الكترود كلافي توسط سيستم تغذيه به سمت نازل تماس هدايت ميشود. فلاكسي كه داخل يك مخزن مخصوص ذخيره شده، از طريق يك لوله انعطاف پذير خرطومي شكل به صورت ثقلي به سمت پايين سرازيـر شده و به جلـوي قوس الكتريكي و يا اطراف آن هدايت ميگردد. بعضي از دستگاهها مجهز به كليد انتخاب نوع جريان مستقيم يا متناوب هستند. نوع جريان و قطبيت بر ميزان نفوذ و پروفيل جوش تأثيرگذار ميباشد. گاهي اوقات در فرآيند SAW از چند الكترود بجاي يك الكترود استفاده ميشود. ايـن موضوع سبب افزايش نرخ رسوب و سرعت جوشكاري ميگردد. فرآيند SAW كاربردهاي گستردهاي دارد. يكي از آنها عمليات سطحي (Surfacing) روي فلزات ميباشد. به عنوان مثال زماني كه مقاومت به خوردگي يا مقاومت به سايش مورد نياز باشد، استفاده از يك فلز غير مقاوم كه با روش SAW توسط يك آلياژ مقاوم پوشش كاري شده است، بسيار اقتصاديتر ميباشد. در ايـن موارد جهت افزايـش بازده، عموماً از الكترودهاي تسمهاي شكل استفاده ميشود.
شايد مهمترين مزيت فرآيند SAW در مقايسه با ساير روشهاي معمول جوشكاري، نرخ رسوب بالا در اين روش ميباشد. در اين فرآيند به دليل مدفون بودن قوس الكتريكي در زير فلاكس، نيازي به استفاده از شيشه تيره جهت محافظت چشمها نميباشد. همچنين ميزان دودهاي توليد شده در حين جوشكاري در مقايسه با بعضي روشهاي ديگر كمتر است. مزيت عمده ديگر اين فرآيند، نفوذ جوش زياد ميباشد، كه اين فرآيند را جهت جوشكاري مقاطع ضخيم مناسب نموده است.
محدوديت اصلي اين روش، امكان جوشكاري فقط در وضعيت تخت ميباشد. همچنين گاهي اوقات از اين روش در جوشهاي نبشي (Fillet) در وضعيت افقي نيز استفاده ميگردد. در صورتيكه در وضعيتهايي غير از موارد فوق، نياز به استفاده از اين فرآيند باشد، ميبايد با تجهيزاتي خاص فلاكس را روي حوضچه مذاب نگهداري نماييم. محدوديت بعدي اين فرآيند، نياز به استفاده از فيكسچرها و وضعيت دهندهها ميباشد. به دليل تشكيل سرباره روي سطح جوش، نياز به تميزكاري در هر پاس ضروري است. درصورتيكه پارامترهاي جوشكاري بطور مناسبي تنظيم نشده باشند، جدا كردن سرباره از سطح به سختي صورت ميپذيرد. نهايتاً به دليل اينكه باراني از فلاكس، قوس الكتريكي را ميپوشاند، مشاهده محل دقيق قوس و حوضچه مذاب در محل اتصال امكان پذير نيست. در اين مواقع پيشنهاد ميگردد قبل از شروع جوشكاري يكبار كل مسير اتصال توسط تراك پيموده شود تا از حركت مناسب آن در حين جوشكاري اطمينان حاصل گردد.